Ensaio Não Destrutivo Correntes Parasitas: Como Garantir a Integridade Estrutural de Equipamentos
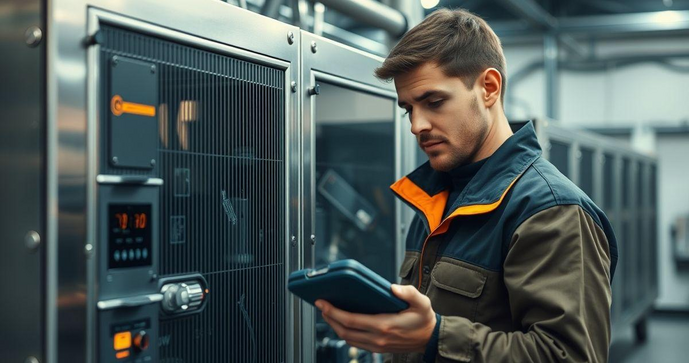
Por: João - 26 de Abril de 2025
O ensaio não destrutivo correntes parasitas é uma técnica fundamental na avaliação da integridade de equipamentos industriais. Este método permite identificar falhas e desgastes sem comprometer a estrutura do material, garantindo a segurança e a eficiência operacional. Neste artigo, exploraremos a importância desse tipo de ensaio, os métodos utilizados para a detecção de correntes parasitas, suas vantagens e as aplicações práticas que demonstram sua relevância no setor industrial.
Importância do Ensaio Não Destrutivo em Equipamentos Industriais
O ensaio não destrutivo (END) é uma técnica essencial na indústria moderna, permitindo a avaliação da integridade de materiais e estruturas sem causar danos permanentes. Essa abordagem é especialmente relevante em setores onde a segurança e a confiabilidade dos equipamentos são cruciais, como na indústria petroquímica, de energia, construção civil e transporte. O uso de ensaios não destrutivos ajuda a identificar falhas ocultas, desgastes e outros problemas que podem comprometer a operação e a segurança dos equipamentos.
Uma das principais vantagens do ensaio não destrutivo é a capacidade de realizar inspeções em componentes críticos sem a necessidade de desmontagem ou interrupção das operações. Isso resulta em economia de tempo e custos, além de minimizar o impacto nas atividades produtivas. Por exemplo, em uma planta industrial, a realização de um ensaio não destrutivo pode ser feita enquanto os equipamentos estão em funcionamento, permitindo que a produção continue sem interrupções significativas.
Além disso, o ensaio não destrutivo é uma ferramenta valiosa para a manutenção preditiva. Ao monitorar a condição dos equipamentos de forma contínua, as empresas podem antecipar falhas e realizar manutenções programadas, evitando paradas inesperadas e custos elevados com reparos emergenciais. Essa abordagem não apenas melhora a eficiência operacional, mas também aumenta a vida útil dos ativos, resultando em um retorno sobre o investimento mais significativo.
Os métodos de ensaio não destrutivo incluem diversas técnicas, como ultrassom, radiografia, líquidos penetrantes e, claro, a detecção de correntes parasitas. Cada um desses métodos possui suas particularidades e é adequado para diferentes tipos de materiais e aplicações. Por exemplo, a técnica de ultrassom é amplamente utilizada para detectar descontinuidades internas em metais, enquanto a radiografia é eficaz na identificação de falhas em soldas e estruturas complexas.
A detecção de correntes parasitas, em particular, é uma técnica que se destaca na avaliação de componentes elétricos e magnéticos. Essa abordagem permite identificar perdas de energia e aquecimento excessivo em equipamentos, o que pode levar a falhas catastróficas se não for tratado adequadamente. Através do ensaio não destrutivo, é possível monitorar a eficiência dos sistemas elétricos e garantir que os equipamentos operem dentro dos parâmetros ideais.
Outro aspecto importante do ensaio não destrutivo é a conformidade com normas e regulamentos de segurança. Muitas indústrias são obrigadas a seguir diretrizes rigorosas para garantir a segurança de seus produtos e processos. A realização de ensaios não destrutivos é frequentemente uma exigência para a certificação de qualidade e segurança, assegurando que os equipamentos atendam aos padrões estabelecidos. Isso não apenas protege os trabalhadores e o meio ambiente, mas também fortalece a reputação da empresa no mercado.
Além disso, o uso de ensaios não destrutivos pode contribuir para a sustentabilidade das operações industriais. Ao identificar problemas precocemente, as empresas podem evitar desperdícios e reduzir o consumo de recursos. Isso é especialmente relevante em um contexto onde a eficiência energética e a redução de resíduos são prioridades globais. A manutenção adequada dos equipamentos, possibilitada pelos ensaios não destrutivos, resulta em operações mais sustentáveis e responsáveis.
Por fim, a importância do ensaio não destrutivo em equipamentos industriais se reflete na segurança, eficiência e sustentabilidade das operações. As empresas que adotam essa abordagem não apenas protegem seus ativos, mas também garantem a segurança de seus colaboradores e a conformidade com as normas regulatórias. A implementação de ensaios não destrutivos, como o Ensaio de tração corpo de prova , é um passo fundamental para a construção de um ambiente industrial mais seguro e eficiente.
Em resumo, o ensaio não destrutivo é uma prática indispensável na indústria moderna. Sua capacidade de detectar falhas sem causar danos, aliada à sua contribuição para a manutenção preditiva e conformidade regulatória, torna essa técnica uma aliada poderosa na busca por operações mais seguras e eficientes. À medida que as indústrias continuam a evoluir, a importância do ensaio não destrutivo só tende a crescer, consolidando-se como uma prática essencial para a integridade e a segurança dos equipamentos industriais.
Métodos de Detecção de Correntes Parasitas
A detecção de correntes parasitas é uma técnica de ensaio não destrutivo que desempenha um papel crucial na avaliação da integridade de materiais condutores, especialmente em componentes elétricos e magnéticos. As correntes parasitas, também conhecidas como correntes de Foucault, são geradas quando um campo magnético variável induz correntes elétricas em um condutor. Essas correntes podem causar aquecimento e perdas de energia, resultando em falhas catastróficas se não forem detectadas a tempo. Neste contexto, diversos métodos de detecção são utilizados para identificar e quantificar essas correntes, garantindo a eficiência e a segurança dos equipamentos.
Um dos métodos mais comuns para a detecção de correntes parasitas é a técnica de medição de impedância. Este método envolve a aplicação de um campo magnético alternado ao material em teste e a medição da resposta elétrica do material. A impedância do material varia em função da frequência do campo magnético e da presença de correntes parasitas. Ao analisar essas variações, é possível identificar a presença de falhas e determinar a gravidade do problema. A medição de impedância é amplamente utilizada em transformadores, motores e outros equipamentos elétricos, onde a eficiência é fundamental.
Outro método eficaz é a termografia infravermelha. Essa técnica utiliza câmeras térmicas para detectar variações de temperatura em componentes elétricos. Quando correntes parasitas estão presentes, elas geram calor, que pode ser visualizado como pontos quentes na superfície do material. A termografia é uma ferramenta poderosa para a detecção de falhas, pois permite a inspeção rápida e não invasiva de equipamentos em operação. Essa abordagem é especialmente útil em ambientes industriais, onde a manutenção deve ser realizada com o mínimo de interrupção nas operações.
A técnica de ressonância magnética também é utilizada na detecção de correntes parasitas. Este método envolve a aplicação de um campo magnético e a medição da resposta do material em diferentes frequências. A ressonância magnética pode fornecer informações detalhadas sobre a estrutura interna do material e a presença de descontinuidades. Embora essa técnica seja mais complexa e cara, ela oferece uma análise aprofundada que pode ser valiosa em aplicações críticas, como na indústria aeroespacial e na fabricação de equipamentos médicos.
Além dessas técnicas, a medição de campo magnético é outra abordagem utilizada para detectar correntes parasitas. Este método envolve a colocação de sensores magnéticos próximos ao material em teste. Os sensores medem a intensidade do campo magnético gerado pelas correntes parasitas, permitindo a identificação de falhas. Essa técnica é particularmente útil em componentes de grande porte, como geradores e transformadores, onde a detecção precisa é essencial para garantir a segurança e a eficiência.
É importante ressaltar que a escolha do método de detecção de correntes parasitas depende de diversos fatores, incluindo o tipo de material, a geometria do componente e as condições operacionais. Cada técnica possui suas vantagens e limitações, e muitas vezes, uma combinação de métodos é utilizada para obter resultados mais precisos. Por exemplo, a termografia pode ser utilizada em conjunto com a medição de impedância para fornecer uma análise mais abrangente da condição do equipamento.
Além disso, a detecção de correntes parasitas deve ser realizada por profissionais qualificados, que possuam conhecimento técnico e experiência nas técnicas de ensaio. A interpretação dos resultados requer uma compreensão profunda dos princípios físicos envolvidos e das características do material em teste. Isso é fundamental para garantir que as conclusões tiradas a partir dos ensaios sejam precisas e confiáveis.
Outro aspecto a ser considerado é a importância da manutenção regular e da inspeção de equipamentos. A detecção de correntes parasitas é uma parte essencial de um programa de manutenção preditiva, que visa identificar problemas antes que se tornem falhas catastróficas. Ao integrar a detecção de correntes parasitas em um plano de manutenção, as empresas podem aumentar a confiabilidade de seus equipamentos e reduzir custos operacionais.
Por fim, é importante destacar que, embora os ensaios não destrutivos, como a detecção de correntes parasitas, sejam fundamentais para a segurança e a eficiência dos equipamentos, eles não substituem a necessidade de ensaios destrutivos em determinadas situações. Os ensaios destrutivos ainda são necessários para avaliar a resistência e a durabilidade dos materiais em condições extremas. A combinação de ensaios não destrutivos e destrutivos proporciona uma visão abrangente da integridade dos materiais, garantindo que os equipamentos operem de forma segura e eficiente.
Em resumo, a detecção de correntes parasitas é uma técnica vital na manutenção e avaliação de equipamentos industriais. Com uma variedade de métodos disponíveis, as empresas podem escolher a abordagem mais adequada para suas necessidades específicas. A implementação de práticas de detecção eficazes não apenas melhora a segurança e a eficiência, mas também contribui para a sustentabilidade das operações industriais.
Vantagens do Ensaio Não Destrutivo para a Manutenção
O ensaio não destrutivo (END) é uma prática essencial na manutenção de equipamentos e estruturas em diversos setores industriais. Essa abordagem permite a avaliação da integridade de materiais sem causar danos permanentes, o que é fundamental para garantir a segurança e a eficiência operacional. As vantagens do ensaio não destrutivo são numerosas e impactam diretamente a forma como as empresas gerenciam seus ativos. Neste artigo, exploraremos as principais vantagens do END para a manutenção, destacando sua importância na prevenção de falhas e na otimização de processos.
Uma das principais vantagens do ensaio não destrutivo é a capacidade de realizar inspeções sem interromper as operações. Em ambientes industriais, onde a continuidade da produção é crucial, a possibilidade de inspecionar equipamentos enquanto estão em funcionamento é um grande benefício. Isso não apenas minimiza o tempo de inatividade, mas também reduz os custos associados à manutenção. Por exemplo, a realização de um ensaio visual de soldagem pode ser feito rapidamente, permitindo que os operadores identifiquem problemas sem a necessidade de desmontar componentes ou parar a produção.
Outra vantagem significativa do ensaio não destrutivo é a detecção precoce de falhas. Através de técnicas como ultrassom, radiografia e termografia, é possível identificar descontinuidades, desgastes e outros problemas antes que se tornem críticos. Essa abordagem proativa é fundamental para a manutenção preditiva, que visa antecipar falhas e realizar intervenções programadas. Ao detectar problemas em estágios iniciais, as empresas podem evitar paradas inesperadas e custos elevados com reparos emergenciais, aumentando a confiabilidade de seus equipamentos.
Além disso, o ensaio não destrutivo contribui para a segurança dos trabalhadores e do ambiente. Equipamentos que não são inspecionados regularmente podem apresentar riscos significativos, como falhas catastróficas que podem resultar em acidentes. A implementação de ensaios não destrutivos ajuda a garantir que os equipamentos estejam em conformidade com as normas de segurança, protegendo não apenas os operadores, mas também o meio ambiente. A segurança é uma prioridade em qualquer operação industrial, e o END desempenha um papel crucial na mitigação de riscos.
Outra vantagem importante do ensaio não destrutivo é a economia de custos a longo prazo. Embora a implementação de um programa de ensaio não destrutivo possa exigir um investimento inicial, os benefícios financeiros superam amplamente os custos. A redução de paradas não programadas, a extensão da vida útil dos equipamentos e a diminuição dos custos de manutenção são apenas algumas das maneiras pelas quais o END pode resultar em economias significativas. Além disso, a capacidade de realizar inspeções regulares permite que as empresas planejem melhor seus orçamentos de manutenção, evitando surpresas financeiras.
O ensaio não destrutivo também oferece uma abordagem mais sustentável para a manutenção. Ao identificar problemas antes que se tornem críticos, as empresas podem evitar o desperdício de recursos e materiais. Isso é especialmente relevante em um contexto onde a eficiência energética e a redução de resíduos são prioridades globais. A manutenção adequada, possibilitada pelos ensaios não destrutivos, resulta em operações mais sustentáveis e responsáveis, alinhando-se às expectativas de consumidores e reguladores.
Além disso, o uso de ensaios não destrutivos pode melhorar a qualidade dos produtos e serviços oferecidos pelas empresas. Equipamentos bem mantidos e inspecionados regularmente garantem que os produtos finais atendam aos padrões de qualidade exigidos. Isso é particularmente importante em setores como a indústria automotiva, aeroespacial e de alimentos, onde a qualidade e a segurança são fundamentais. A implementação de um programa de ensaio não destrutivo ajuda a construir uma reputação sólida no mercado, aumentando a confiança dos clientes e a competitividade da empresa.
Outro aspecto a ser considerado é a flexibilidade que os ensaios não destrutivos oferecem. Existem diversas técnicas disponíveis, cada uma adequada para diferentes tipos de materiais e aplicações. Isso permite que as empresas escolham a abordagem mais apropriada para suas necessidades específicas. Por exemplo, a termografia pode ser utilizada para detectar falhas térmicas em sistemas elétricos, enquanto a radiografia é eficaz na avaliação de soldas e estruturas complexas. Essa versatilidade torna o ensaio não destrutivo uma ferramenta valiosa em qualquer programa de manutenção.
Por fim, a capacitação e o treinamento de pessoal são aspectos que também se beneficiam do uso de ensaios não destrutivos. A implementação de um programa de END requer profissionais qualificados que compreendam as técnicas e os princípios envolvidos. Isso não apenas melhora a competência da equipe, mas também promove uma cultura de segurança e qualidade dentro da organização. Investir na formação de colaboradores para realizar ensaios não destrutivos é um passo importante para garantir a eficácia do programa de manutenção.
Em resumo, as vantagens do ensaio não destrutivo para a manutenção são amplas e impactam diretamente a segurança, a eficiência e a sustentabilidade das operações industriais. A capacidade de realizar inspeções sem interromper a produção, a detecção precoce de falhas, a economia de custos e a melhoria da qualidade são apenas algumas das razões pelas quais o END é uma prática indispensável. À medida que as indústrias continuam a evoluir, a importância do ensaio não destrutivo só tende a crescer, consolidando-se como uma abordagem essencial para a manutenção eficaz e responsável.
Aplicações Práticas do Ensaio Não Destrutivo Correntes Parasitas
O ensaio não destrutivo (END) por correntes parasitas é uma técnica amplamente utilizada em diversas indústrias para avaliar a integridade de materiais condutores. Essa abordagem permite a detecção de falhas e descontinuidades sem causar danos ao material, o que é essencial para garantir a segurança e a eficiência operacional. As aplicações práticas do ensaio não destrutivo por correntes parasitas são variadas e abrangem setores como energia, transporte, manufatura e construção civil. Neste artigo, exploraremos algumas das principais aplicações dessa técnica.
Uma das aplicações mais comuns do ensaio por correntes parasitas é na indústria de energia, especialmente na inspeção de componentes elétricos e magnéticos. Transformadores, geradores e motores elétricos são frequentemente submetidos a ensaios não destrutivos para identificar falhas que possam comprometer seu desempenho. A detecção de correntes parasitas permite identificar problemas como sobreaquecimento, que pode levar a falhas catastróficas se não for tratado a tempo. Por meio dessa técnica, as empresas podem garantir que seus equipamentos operem de forma eficiente e segura, minimizando o risco de interrupções na produção de energia.
Outra aplicação importante do ensaio não destrutivo por correntes parasitas é na indústria automotiva. Componentes como bobinas de ignição, motores elétricos e sistemas de frenagem são críticos para a segurança e o desempenho dos veículos. A utilização de correntes parasitas para inspecionar esses componentes permite a detecção de falhas internas, como trincas e desgastes, que podem afetar a funcionalidade e a segurança do veículo. Com a crescente demanda por veículos elétricos e híbridos, a importância do ensaio por correntes parasitas na indústria automotiva só tende a aumentar, uma vez que esses veículos dependem fortemente de sistemas elétricos e eletrônicos.
Na indústria aeroespacial, o ensaio não destrutivo por correntes parasitas é utilizado para garantir a integridade de componentes críticos, como fuselagens, asas e motores. A segurança é uma prioridade máxima na aviação, e a detecção precoce de falhas é essencial para evitar acidentes. Os ensaios por correntes parasitas permitem a identificação de descontinuidades em materiais compósitos e metálicos, assegurando que os componentes atendam aos rigorosos padrões de segurança e desempenho exigidos pela indústria. Essa técnica é particularmente valiosa em inspeções de manutenção, onde a integridade estrutural deve ser verificada regularmente.
Além disso, o ensaio não destrutivo por correntes parasitas é amplamente utilizado na fabricação de equipamentos industriais. Máquinas e ferramentas, como prensas, tornos e fresadoras, são frequentemente inspecionadas para garantir que estejam em boas condições de funcionamento. A detecção de falhas em componentes críticos, como rolamentos e engrenagens, pode evitar paradas não programadas e reduzir os custos de manutenção. Ao implementar um programa de ensaio não destrutivo, as empresas podem aumentar a eficiência de suas operações e prolongar a vida útil de seus equipamentos.
Outra aplicação prática do ensaio por correntes parasitas é na construção civil, onde a integridade de estruturas metálicas é fundamental. A detecção de falhas em vigas, colunas e outros elementos estruturais é essencial para garantir a segurança de edifícios e pontes. O ensaio não destrutivo por correntes parasitas permite a identificação de corrosão, trincas e outros problemas que podem comprometer a estabilidade da estrutura. Essa técnica é especialmente útil em inspeções de manutenção, onde a avaliação da condição de estruturas existentes é necessária para garantir a segurança e a durabilidade a longo prazo.
O ensaio não destrutivo por correntes parasitas também é utilizado em aplicações de pesquisa e desenvolvimento. Laboratórios e instituições de pesquisa utilizam essa técnica para estudar as propriedades de novos materiais e desenvolver produtos inovadores. A capacidade de detectar falhas em materiais experimentais sem danificá-los é uma vantagem significativa, permitindo que os pesquisadores avaliem o desempenho e a viabilidade de novos produtos antes de sua produção em larga escala.
Além disso, a combinação do ensaio por correntes parasitas com outras técnicas de ensaio não destrutivo, como o Ultrassom phased array , pode proporcionar uma análise mais abrangente da integridade dos materiais. Essa abordagem integrada permite que as empresas realizem inspeções mais completas e precisas, aumentando a confiabilidade dos resultados e a segurança dos equipamentos.
Em resumo, as aplicações práticas do ensaio não destrutivo por correntes parasitas são diversas e abrangem uma ampla gama de indústrias. Desde a energia até a construção civil, essa técnica desempenha um papel crucial na garantia da integridade e segurança de equipamentos e estruturas. A capacidade de detectar falhas sem causar danos, aliada à sua eficácia na manutenção preditiva, torna o ensaio não destrutivo por correntes parasitas uma ferramenta indispensável para as empresas que buscam otimizar suas operações e garantir a segurança de seus ativos. À medida que a tecnologia avança, espera-se que o uso de ensaios não destrutivos continue a crescer, proporcionando soluções cada vez mais eficazes para a detecção de falhas e a manutenção de equipamentos.
Em conclusão, o ensaio não destrutivo por correntes parasitas se destaca como uma ferramenta essencial para a manutenção e a segurança de equipamentos industriais. Sua capacidade de detectar falhas sem causar danos ao material não apenas assegura a integridade estrutural, mas também contribui para a eficiência operacional e a redução de custos. As diversas aplicações práticas dessa técnica em setores como energia, automotivo, aeroespacial e construção civil evidenciam sua importância na prevenção de falhas catastróficas e na promoção de operações seguras e sustentáveis. À medida que as indústrias continuam a evoluir, a adoção de ensaios não destrutivos se tornará cada vez mais crucial para garantir a confiabilidade e a segurança dos ativos, consolidando-se como uma prática indispensável no cenário industrial moderno.