Ensaio Não Destrutivo em Correntes Parasitas
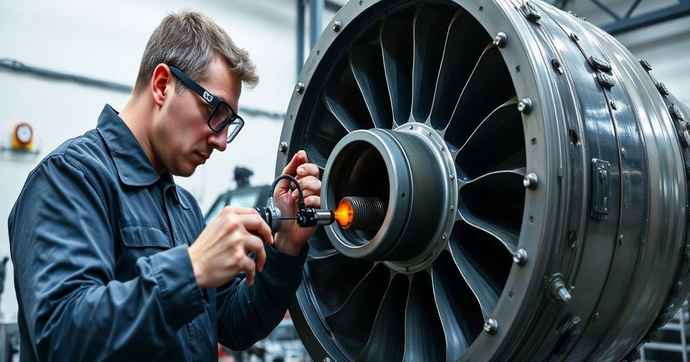
Por: João - 30 de Dezembro de 2024
O ensaio não destrutivo correntes parasitas é uma técnica crucial para a avaliação da integridade de materiais sem comprometê-los. Este método permite identificar falhas internas e garantir a segurança e eficiência de equipamentos em diversas indústrias. Neste artigo, vamos explorar o que são correntes parasitas, a importância dos ensaios não destrutivos e suas principais aplicações. Acompanhe para entender como essa abordagem pode beneficiar sua empresa e melhorar a segurança operacional.
O que são correntes parasitas?
Correntes parasitas são correntes elétricas indesejadas que são geradas em materiais condutores quando estes são expostos a um campo magnético variável. Esse fenômeno ocorre devido ao princípio da indução eletromagnética, descrito pela lei de Faraday, que estabelece que uma variação no fluxo magnético através de um circuito induz uma corrente elétrica nesse circuito. As correntes parasitas podem provocar aquecimento em materiais e, em alguns casos, até danificá-los, resultando em falhas estruturais.
Essas correntes são chamadas de "parasitas" porque, ao contrário das correntes que desempenham uma função desejada, como aquelas que alimentam máquinas elétricas, elas não beneficiam o sistema. Em vez disso, representam uma perda de energia e podem interferir no desempenho adequado de componentes metálicos e equipamentos que utilizam materiais condutores. Por isso, a detecção e controle de correntes parasitas são essenciais, especialmente em aplicações industriais onde a segurança e a eficiência são prioridades.
O estudo das correntes parasitas é especialmente relevante em áreas como engenharia elétrica e materiais, pois permite aos especialistas entenderem melhor como essas correntes se desenvolvem e como mitigá-las eficazmente. Elas podem ser especialmente problemáticas em componentes sujeitos a variações magnéticas, como transformadores, motores elétricos e indutores.
Um dos principais desafios relacionados às correntes parasitas é que elas podem causar aquecimento excessivo em materiais. Esse aquecimento pode resultar em distorções, degradação das propriedades mecânicas e até mesmo falhas catastróficas. Por essa razão, o monitoramento e a análise de correntes parasitas são vital para garantir a integridade e o funcionamento seguro de muitos dispositivos e sistemas elétricos.
Felizmente, técnicas modernas de ensaio não destrutivo, como o Ultrassom phased array, podem ser utilizadas para identificar e escolher os métodos mais apropriados para a detecção de correntes parasitas em diversos materiais. Esses métodos permitem uma inspeção precisa sem prejudicar a integridade dos materiais, garantindo assim que eles possam continuar a funcionar adequadamente.
Uma das aplicações mais comuns para o monitoramento de correntes parasitas é em sistemas de transporte, como trens de levitação magnética e trens de carga. Nestes sistemas, o controle rigoroso das correntes parasitas é necessário para evitar superaquecimentos que poderiam levar a falhas mecânicas. Os sistemas que detectam essas correntes, bem como os que utilizam tecnologia de monitoramento, permitem que engenheiros e operadores identifiquem problemas antes que eles se tornem sérios.
Além disso, as correntes parasitas também desempenham um papel importante na fabricação de equipamentos eletrônicos. Componentes como resistores e capacitores precisam ser projetados para minimizar o impacto das correntes parasitas. Isso é feito empregando técnicas de design e escolha de materiais que reduzem a indução de correntes parasitas em circuitos eletrônicos. A compreensão de como as correntes parasitas interagem com esses componentes pode levar a um desenvolvimento mais eficiente e seguro de novos produtos eletrônicos.
Outro contexto em que as correntes parasitas são significativas é nas estruturas metálicas das construções. Ao examinar estruturas como pontes e edifícios, engenheiros utilizam ensaios não destrutivos para garantir que não haja dúvidas quanto à integridade dos materiais utilizados. A detecção de correntes parasitas é parte desse processo, pois indica que poderá haver potenciais problemas com a estrutura que poderiam comprometer a segurança e a longevidade da construção.
Portanto, compreender o que são correntes parasitas é fundamental para profissionais de diversas áreas, especialmente na engenharia e na indústria. A análise e o gerenciamento eficaz dessas correntes podem resultar em melhorias significativas em segurança, eficiência e confiabilidade de sistemas elétricos e mecânicos. Com o avanço das tecnologias, como os ensaios não destrutivos, a detecção e a mitigação de correntes parasitas tornam-se cada vez mais acessíveis, assegurando a integridade dos materiais e a segurança operacional.
Importância do ensaio não destrutivo
O ensaio não destrutivo (END) é uma técnica essencial para a avaliação de materiais e estruturas sem causar qualquer dano a eles. Essa abordagem inovadora permite a inspeção e a análise de componentes metálicos, plásticos e de outros materiais, garantindo a qualidade e a segurança de produtos e sistemas presentes em diversas indústrias. A importância do ensaio não destrutivo se estende a diversos setores, como a construção civil, a indústria automotiva, a aeronáutica e a produção de energia, onde a integridade estrutural é fundamental para o funcionamento adequado e seguro das operações.
Uma das principais vantagens do ensaio não destrutivo é sua capacidade de detectar falhas internas, fissuras, trincas e outros defeitos que podem não ser visíveis à olho nu. Com o uso de técnicas como ultrassom, raios X e ensaio visual de soldagem, os profissionais podem identificar problemas que, se não detectados, poderiam levar a falhas catastróficas. Isso é especialmente crítico em indústrias onde a segurança é uma prioridade máxima, como no setor aeroespacial, onde qualquer falha pode ter consequências desastrosas.
Além de garantir a segurança, o ensaio não destrutivo também contribui para a eficiência e a economia nas operações industriais. Ao detectar problemas precocemente, as empresas podem evitar reparos dispendiosos ou substituições prematuras de equipamentos. Isso reduz custos operacionais e aumenta a vida útil dos ativos. Em um ambiente industrial cada vez mais competitivo, a minimização de gastos e a maximização da eficiência são essenciais para o sucesso de uma empresa.
A aplicação do ensaio não destrutivo também pode ser vista em processos de manutenção preditiva, onde a monitorização constante dos equipamentos permite que os operadores realizem intervenções antes que uma falha ocorra. Esse tipo de abordagem é vantajosa porque permite que as empresas planejem paradas programadas para manutenção, evitando quebras inesperadas e os custos associados a elas. Além disso, isso ajuda a manter a produção em níveis otimizados, pois os equipamentos permanecem em funcionamento por mais tempo.
Outro aspecto importante do ensaio não destrutivo é sua contribuição para a conformidade com regulamentações e normas de qualidade. O cumprimento de padrões como ISO 9001 e ASTM é essencial para muitas indústrias, e o uso de END oferece uma maneira de garantir que os produtos atendam a esses critérios. Com a utilização de técnicas adequadas de ensaio não destrutivo, as empresas podem assegurar que estão operando dentro das diretrizes regulamentares, minimizando o risco de sanções e melhorando a reputação no mercado.
As técnicas de ensaio não destrutivo também promovem a inovação na indústria. À medida que novos materiais são desenvolvidos e utilizados em produtos modernos, as empresas precisam adaptar suas práticas de inspeção para garantir que essas inovações sejam seguras e confiáveis. O END permite que engenheiros e técnicos experimentem novos materiais, como compósitos e ligas metálicas, sem comprometer a integridade dos componentes, o que leva a um aumento da inovação e à criação de soluções ainda mais eficazes.
Na indústria da construção civil, o ensaio não destrutivo é fundamental para garantir a integridade de estruturas. Através de métodos como a ultrassonografia e os ensaios de vazamento, é possível avaliar a qualidade do concreto, identificar falhas nas soldagens e garantir que os materiais utilizados estejam em conformidade com as especificações. Isso não apenas assegura a segurança dos edifícios, mas também aumenta a durabilidade e reduz custos relacionados a reparos e manutenções futuras.
Além disso, a utilização de métodos não destrutivos pode contribuir para a sustentabilidade ambiental. Ao prolongar a vida útil dos materiais e estruturas, as empresas podem reduzir o desperdício e minimizar a necessidade de extração de novos recursos. Essa abordagem sustentável é cada vez mais relevante em um mundo que prioriza práticas empresariais responsáveis e preocupadas com o meio ambiente.
Por fim, a importância do ensaio não destrutivo está intrinsecamente ligada à proteção da vida humana e dos ativos materiais. Em um mundo onde a segurança, a eficiência e a inovação são primordiais, o END se destaca como uma ferramenta valiosa. Seja na prevenção de desastres catastróficos ou na otimização de processos, o ensaio não destrutivo demonstra não apenas seu valor econômico, mas também seu papel crítico na promoção de um ambiente de trabalho mais seguro e eficiente.
Principais técnicas de ensaio não destrutivo
Os ensaios não destrutivos (END) são fundamentais para a avaliação da integridade de materiais e estruturas sem causar danos a elas. As técnicas de END empregam diferentes princípios físicos para detectar e avaliar falhas, trincas, corrosão e outros defeitos em componentes. Cada técnica tem suas particularidades e é adequada para aplicações específicas. Neste artigo, exploraremos as principais técnicas de ensaio não destrutivo, destacando seus métodos, aplicações e benefícios.
Uma das mais comuns e amplamente utilizadas técnicas de ensaio não destrutivo é o teste ultrassônico. Esse método utiliza ondas sonoras de alta frequência para penetrar no material. Quando essas ondas encontram uma descontinuidade, como uma trinca, parte da onda é refletida de volta para o transdutor, que então converte essas ondas de retorno em sinais elétricos. O processamento desses sinais permite aos engenheiros identificar a localização e a dimensão das falhas. O teste ultrassônico é altamente preciso e pode ser utilizado em uma variedade de materiais, incluindo metais, plásticos e compósitos, tornando-se uma escolha popular em setores como a aeronáutica e a indústria automotiva.
Outra técnica importante é o radiográfico, que utiliza raios X ou raios gamma para inspecionar materiais. Durante o processo, uma fonte de radiação é posicionada de um lado do componente, enquanto um detector de radiação é posicionado do outro lado. Se houver falhas internas, a radiação será atenuada de maneira diferente, resultando em uma imagem radiográfica que revela a estrutura interna do material. O ensaio radiográfico é especialmente útil para identificar vazamentos, trincas e inclusões em vários tipos de materiais e é amplamente utilizado em testes de soldagens e em estruturas metálicas.
O ensaio por líquido penetrante é outra técnica efetiva, que envolve a aplicação de um líquido com alta tensão superficial sobre a superfície do componente. Após um período de penetração, o excesso de líquido é removido, e um revelador é aplicado para destacar as falhas que podem ter absorvido o líquido. Essa técnica é particularmente eficaz em detectar falhas superficiais e é frequentemente utilizada em produtos metálicos, sendo uma abordagem de baixo custo. É importante mencionar que, embora esse método seja simples, ele requer preparação adequada da superfície e interpretação precisa dos resultados.
O ensaio magnético é uma técnica que se utiliza da propriedade magnética dos materiais ferromagnéticos. Neste método, um campo magnético é gerado em um componente. Se houver uma descontinuidade, como uma trinca, as linhas de fluxo magnético serão desviadas, resultando em um padrão que pode ser visualizado com o uso de partículas magnéticas. Essa técnica é comumente utilizada para verificar soldas e outras áreas críticas em peças metálicas, sendo eficaz para detectar falhas superficiais e próximas à superfície.
O teste de ondas eletromagnéticas também é uma técnica de ensaio não destrutivo. Nesse método, são utilizadas ondas eletromagnéticas para avaliar a integridade de materiais. A principal vantagem desse método é sua capacidade de inspecionar materiais a altas velocidades, sendo adequado para detecções rápidas em processos de produção. É frequentemente aplicado na monitoração de tubulações e componentes em indústrias de petróleo e gás.
Outras técnicas modernas como a termografia infravermelha têm ganhado espaço no mercado de ensaios não destrutivos. Este método analisa a radiação térmica emitida por um objeto para identificar padrões de temperatura que podem indicar falhas, como isolamento deficiente ou áreas de superaquecimento. A termografia é usada principalmente na inspeção de sistemas elétricos e mecânicos, além de ser eficaz na detecção de infiltrações em edifícios.
A fusão de várias técnicas também é uma tendência em ensaios não destrutivos. A combinação de métodos como ultrassom e radiografia pode oferecer resultados mais completos e confiáveis. Essa abordagem multisensorial permite que os engenheiros tenham uma visão mais holística da integridade estrutural de um componente, resultando em avaliações mais precisas e fundamentadas.
Embora cada técnica de ensaio não destrutivo tenha suas virtudes, é fundamental reconhecer que a escolha do método ideal depende de diversos fatores, incluindo o tipo de material, a configuração da peça, o tipo de defeito a ser detectado e os requisitos de inspeção. Por exemplo, em aplicações onde a estética e a aparência superficial são cruciais, o ensaio visual pode ser a melhor opção, enquanto em casos onde a segurança é a principal preocupação, como em estruturas críticas, técnicas de alta precisão como o ultrassom ou radiografia podem ser mais apropriadas.
Por fim, é importante destacar que os ensaios não destrutivos apresentam vantagens significativas em relação aos ensaios destrutivos, pois permitem que os materiais sejam avaliados sem comprometê-los, prolongando sua vida útil e assegurando a segurança e eficiência nos processos industriais. A escolha do método adequado e a correta interpretação dos resultados são essenciais para garantir a eficácia das inspeções e a integridade dos componentes analisados. A cada dia, novas inovações e melhorias nas tecnologias de END estão surgindo, aumentando ainda mais sua relevância e importância no mercado atual.
Aplicações do ensaio em correntes parasitas
As correntes parasitas são um fenômeno elétrico que ocorre em materiais condutores quando expostos a campos magnéticos alternados. A avaliação e o controle dessas correntes são fundamentais em diversas aplicações industriais, especialmente na prevenção de falhas materiais que podem comprometer a segurança e a eficiência operacional. O ensaio não destrutivo (END) aplicado às correntes parasitas tem se mostrado uma ferramenta valiosa em várias indústrias. Neste artigo, discutiremos as principais aplicações do ensaio em correntes parasitas e como ele contribui para a melhoria dos processos produtivos.
Uma das áreas onde a aplicação de ensaios em correntes parasitas é crucial é na indústria de transformação metalúrgica. Durante a fabricação de componentes metálicos, é fundamental garantir que não haja descontinuidades ou falhas que possam afetar o desempenho do produto final. O ensaio de correntes parasitas pode ser usado para detectar problemas como falhas na soldagem, microfissuras ou desgastes em materiais, assegurando a qualidade dos produtos. Essa técnica é especialmente importante em indústrias onde a segurança é prioridade, como na fabricação de peças para a indústria automotiva e aeroespacial.
Além disso, o ensaio em correntes parasitas é amplamente utilizado na manutenção de equipamentos elétricos e eletromecânicos. Em motores, geradores e transformadores, as correntes parasitas podem causar aquecimento excessivo, levando a danos e falhas operacionais. Através de técnicas de ensaio não destrutivo, é possível monitorar a presença de correntes parasitas e identificar condições anormais antes que ocorram falhas graves. Isso permite que as organizações programem manutenções preventivas, reduzindo custos e melhorando a confiabilidade dos sistemas.
Outro campo de aplicação relevante é na engenharia civil, especialmente na análise da integridade de estruturas metálicas. As correntes parasitas são frequentemente utilizadas para avaliar a condição de pontes, torres e edifícios. O ensaio permite detectar corrosão, desgastes e outras falhas que possam comprometer a segurança estrutural. Essa prática não apenas garante a segurança de construções, mas também é essencial para a manutenção da certificação e conformidade com regulamentos de segurança. A estrutura de uma ponte, por exemplo, deve ser inspecionada regularmente para garantir que não haja danos ocultos que possam levar a uma catástrofe.
Na área de energia, o ensaio em correntes parasitas é aplicado na avaliação de equipamentos como discos de freio de usinas eólicos e componentes de turbinas. Durante a operação, esses componentes estão sujeitos a campos magnéticos intensos e, consequentemente, a correntes parasitas. O monitoramento por meio de ensaios não destrutivos pode revelar a presença de flutuações que indicam degradação ou danos nos materiais, permitindo a correção antes que se transformem em falhas mecânicas. Isso se traduz em maior eficiência na geração de energia e diminuição do tempo de inatividade das máquinas.
Outra aplicação importante dos ensaios em correntes parasitas é na indústria ferroviária. Trens e sistemas de transporte ferroviário de alta velocidade dependem da integridade de suas componentes metálicas. A avaliação com ensaios não destrutivos pode assegurar que não existam trincas, fraturas ou desgastes que possam ameaçar a segurança dos passageiros. Com o uso de correntes parasitas, as operadoras ferroviárias podem monitorar a condição dos trilhos, vagões e locomotivas, permitindo a realização de manutenções antes que problemas sérios ocorram.
A área de pesquisa e desenvolvimento também se beneficia com a aplicação de ensaios em correntes parasitas. Universidades e laboratórios estão sempre inovando, desenvolvendo novos materiais e tecnologias. Testes de correntes parasitas são essenciais para validar a performance e a durabilidade desses novos materiais e sistemas. Ensaios não destrutivos ajudam os pesquisadores a entender comportamentos inesperados e a corrigir problemas antes que os produtos cheguem ao mercado.
Um aspecto significativo da aplicação dos ensaios em correntes parasitas é a capacidade de integrar esse método com outras abordagens de avaliação. Por exemplo, muitas indústrias utilizam o ensaio de tração em conjunto com ensaios de correntes parasitas, a fim de obter uma visão mais profunda da integridade do material. Essa combinação de técnicas pode resultar em análises mais precisas e inovações em procedimentos de inspeção.
Em resumo, as aplicações do ensaio em correntes parasitas são amplamente diversificadas e essenciais para garantir a segurança, eficiência e durabilidade de componentes em várias indústrias. Desde a fabricação até a manutenção, o uso deste tipo de ensaio não destrutivo se mostra imprescindível. Da detecção de falhas em estruturas metálicas à garantia de funcionalidade em sistemas críticos de energia, os ensaios em correntes parasitas não só aumentam a confiança dos engenheiros nas condições de operação, mas também promovem um ambiente industrial mais seguro e eficiente. Com o desenvolvimento contínuo de novas tecnologias e métodos de ensaio, as possibilidades para o uso de ensaios em correntes parasitas só tendem a crescer e expandir-se nas indústrias do futuro.
Vantagens do ensaio não destrutivo
O ensaio não destrutivo (END) é uma técnica fundamental utilizada em diferentes setores industriais para garantir a qualidade e a integridade de materiais e estruturas. Através de métodos que não causam dano aos componentes analisados, os ensaios não destrutivos oferecem diversas vantagens que contribuem para a segurança, eficiência e confiabilidade das operações. Neste artigo, discutiremos as principais vantagens do ensaio não destrutivo e como elas impactam positivamente as diferentes indústrias.
Uma das vantagens mais significativas do END é a preservação da integridade dos materiais. Ao contrário de ensaios destrutivos, que comprometem o material testado, os ensaios não destrutivos permitem a análise de componentes sem causar qualquer dano. Isso é essencial em indústrias onde a continuidade operacional é um requisito. Por exemplo, em setores como a energia e a aeronáutica, onde cada componente deve funcionar de forma confiável, o END se torna uma ferramenta valiosa para garantir que tudo esteja nas melhores condições sem a necessidade de substituições dispendiosas.
A detecção precoce de falhas é outra vantagem importante dos ensaios não destrutivos. Essas técnicas permitem que as organizações identifiquem problemas em seus materiais antes que eles se agravem, evitando falhas catastróficas e custos operacionais elevados. Por meio de inspeções regulares, é possível monitorar a condição dos equipamentos e garantir que qualquer anomalia seja corrigida antes que cause danos maiores. Isso é particularmente relevante em ambientes de alta demanda, como em linhas de produção, onde paradas não planejadas podem resultar em perda de receitas significativas.
O ensaio não destrutivo também promove a economia de custos. Embora a implementação inicial de técnicas de END possa parecer dispendiosa, a longo prazo, o retorno sobre o investimento é considerável. Ao evitar falhas mecânicas e reparos inesperados, as empresas conseguem minimizar gastos com manutenção e substituição de equipamentos. Além disso, a análise eficiente dos materiais permite que as empresas maximizem a vida útil de seus ativos e, por consequência, reduzam a necessidade de comprar novos componentes com frequência.
Escolher o método de ensaio não destrutivo correto também oferece flexibilidade. Existem diversas técnicas disponíveis, como ensaio ultrassônico, radiográfico, de líquido penetrante e magnético, entre outros. Isso permite que os engenheiros selecionem a melhor abordagem de acordo com suas necessidades específicas e os materiais que estão sendo analisados. Essa adaptabilidade torna o END útil em uma variedade de aplicações, desde a construção civil até a indústria petroquímica, sempre que for necessário garantir a segurança e qualidade de componentes críticos.
Os ensaios não destrutivos também são benéficos para a conformidade com normas e regulamentos. Muitas indústrias estão sujeitas a rigorosos padrões de segurança e qualidade. A utilização de END, que fornece dados confiáveis sobre a integridade dos materiais, ajuda as empresas a manterem-se em conformidade com as regulamentações e a evitarem sanções legais. Isso se aplica a setores onde a segurança do consumidor e a proteção do meio ambiente são prioritárias, como na indústria alimentícia e farmacêutica.
Além disso, as técnicas de ensaio não destrutivo são essenciais para a sustentabilidade ambiental. Ao prolongar a vida útil dos materiais e estruturas, o END reduz a quantidade de resíduos gerados e minimiza a necessidade de produção de novos materiais. Essa abordagem ecoeficiente é vital em uma era em que a sustentabilidade é uma preocupação crescente em muitas indústrias. O uso de ensaios não destrutivos pode ajudar empresas a adotarem práticas mais responsáveis em relação ao meio ambiente.
Outro aspecto importante a ser considerado é a capacidade de realizar medições em ambientes de trabalho perigosos. Muitas vezes, a avaliação de componentes críticos deve ocorrer em locais onde é impossível realizar ensaios destrutivos devido a riscos de segurança. Os métodos não destrutivos permitem a realização de avaliações em condições adversas, garantindo a segurança dos trabalhadores. Essa vantagem é particularmente relevante em indústrias como petróleo e gás, onde a segurança do ambiente operacional é uma prioridade.
Além de todas essas vantagens, o ensaio não destrutivo oferece a possibilidade de testes em tempo real. Isso significa que os engenheiros podem monitorar a condição dos materiais instantaneamente, em vez de esperar por resultados de testes que podem demorar dias. Essa capacidade de resposta rápida permite que ajustes possam ser feitos com mais agilidade e eficiência, melhorando ainda mais o fluxo produtivo.
Por fim, a utilização de ensaios não destrutivos também proporciona uma oportunidade para formação e desenvolvimento profissional. A equipe que realiza esses ensaios precisa de conhecimentos técnicos específicos, o que promove a capacitação contínua dos colaboradores. Isso não só aumenta a qualidade do trabalho, mas também eleva o moral da equipe ao saber que está contribuindo para a segurança e integridade operacional da empresa.
Em resumo, as vantagens do ensaio não destrutivo se traduzem em uma ferramenta imprescindível para a indústria moderna. Desde a preservação da integridade dos materiais até a detecção precoce de falhas e a economia de custos, o END desempenha um papel fundamental na manutenção de altos padrões de segurança e qualidade. Com a crescente necessidade de eficiência e sustentabilidade, o uso de ensaios não destrutivos tende a se expandir, contribuindo assim para um futuro industrial mais seguro e sustentável.
Diferenças entre ensaios destrutivos e não destrutivos
Os ensaios destrutivos e não destrutivos são técnicas de avaliação utilizadas para testar a qualidade e a integridade de materiais e estruturas. Ambas têm suas aplicações, vantagens e desvantagens. No entanto, as diferenças entre essas abordagens são fundamentais para a escolha do método mais apropriado em um projeto específico. Neste artigo, vamos explorar as principais diferenças entre ensaios destrutivos e não destrutivos, ajudando a esclarecer em que situações cada um é mais adequado.
A primeira e mais evidente diferença entre os dois tipos de ensaio é que os ensaios destrutivos (ED) envolvem a aplicação de forças ou condições que levam os materiais a falharem, enquanto os ensaios não destrutivos (END) são projetados para avaliar a integridade dos materiais sem causar dano. Por exemplo, um ensaio de tração, que classifica um material testando sua resistência à ruptura, é considerado um ensaio destrutivo, pois o material é fisicamente comprometido durante o teste. Por outro lado, técnicas como ultrassom, raios X e ensaio visual são exemplos de ensaios não destrutivos, que permitem a análise de um componente sem alterar suas propriedades físicas e funcionais.
A natureza de cada ensaio implica também em diferentes objetivos de teste. Os ensaios destrutivos são tipicamente realizados para determinar propriedades mecânicas dos materiais, como resistência, dureza e ductilidade. Eles são essenciais no desenvolvimento de novos materiais, na avaliação de conformidade com normas e na validação de processos de fabricação. Já os ensaios não destrutivos têm como foco a detecção de falhas, desgastes e descontinuidades em materiais já utilizados e em operação. O objetivo é garantir a integridade estrutural e a segurança dos componentes sem a necessidade de destruição.
Outra diferença importante entre essas duas abordagens é o custo associado a cada uma. Ensaios destrutivos podem resultar em custos mais altos, pois o material testado é inviabilizado após a avaliação. Isso significa que, especialmente em situações onde o componente é caro ou difícil de substituir, pode haver impactos financeiros significativos. Em contrapartida, os ensaios não destrutivos tendem a ser mais econômicos no longo prazo, pois possibilitam que o material continue em uso após as avaliações, evitando a necessidade de substituições recorrentes. Essa economia é um fator que muitas empresas consideram importante ao planejar seus processos de controle de qualidade.
A aplicação e o escopo dos ensaios também variam substancialmente. Ensaios destrutivos são comumente utilizados na fase inicial de desenvolvimento de produtos e podem ser aplicados em laboratórios para a análise de propriedades materiais. Eles são críticos em pesquisa e desenvolvimento e são frequentemente utilizados para a caracterização de novos materiais. Por outro lado, os ensaios não destrutivos são amplamente utilizados durante a produção em massa e também na manutenção de ativos existentes. Isso se aplica a diversas indústrias, incluindo construção civil, petroquímica, aço e aeronáutica, onde a integridade dos componentes é vital para a segurança e a eficiência operacional.
Além disso, os ensaios destrutivos normalmente requerem mais tempo para a preparação e análise. Durante um ensaio destrutivo, é necessário criar amostras, realizar testes em diferentes condições e interpretar os resultados de forma abrangente. Por outro lado, o END pode ser executado com maior rapidez, possibilitando inspeções em tempo real em ambientes industriais, levando a uma resposta mais ágil quanto a problemas detectados. Um exemplo prático dessa agilidade é visível quando se considera a inspeção de um duto de petróleo: testes não destrutivos podem ser realizados rapidamente, permitindo que a produção continue enquanto a integridade é monitorada.
Ademais, enquanto os ensaios destrutivos geralmente fornecem informações detalhadas a respeito das características do material, como resistência e elasticidade, os ensaios não destrutivos tendem a fornecer uma visão mais global do estado do componente. Isso significa que, apesar de os ED serem mais adequados para determinar propriedades fundamentais, os END são imprescindíveis para a análise da condição atual e a confiabilidade dos ativos durante sua vida útil.
Outra questão a ser considerada é a regulamentação e a certificação. Muitas indústrias têm normas específicas que exigem a realização de ensaios não destrutivos para garantir a segurança. Essas exigências podem variar de acordo com o tipo de material e aplicação. Por exemplo, na indústria da aviação, os componentes são frequentemente submetidos a ensaios não destrutivos para garantir que cada peça atenda aos padrões de segurança mais rigorosos. Em contraste, os ensaios destrutivos são mais comuns em processos de fabricação de materiais estruturais, onde sua aplicação é parte do controle de qualidade inicial.
Em resumo, a diferença entre ensaios destrutivos e não destrutivos é fundamental para o controle de qualidade em várias indústrias. Enquanto os ensaios destrutivos são essenciais para determinar propriedades mecânicas e caracterizar materiais, os ensaios não destrutivos são vitais para assegurar a integridade e a segurança de componentes em operação. A escolha entre esses métodos depende das necessidades específicas de cada projeto, custo, tempo e objetivo desejado. Assim, compreender essas diferenças é crucial para engenheiros e técnicos que buscam garantir a qualidade e a confiabilidade de produtos e estruturas em diversos setores.
Desafios no uso de correntes parasitas
As correntes parasitas são fenômenos indesejados que ocorrem em materiais condutores quando expostos a campos magnéticos alternados. Enquanto o uso dessas correntes pode ser benéfico em algumas aplicações, também apresenta uma série de desafios que precisam ser abordados. Neste artigo, discutiremos os principais desafios associados ao uso de correntes parasitas em diferentes campos e como esses desafios podem ser mitigados por meio de práticas adequadas de controle e monitoramento.
Um dos maiores desafios relacionados ao uso de correntes parasitas diz respeito ao aquecimento excessivo que elas podem causar. Quando um material condutor é sujeito a um campo magnético alternado, correntes indesejadas podem ser geradas, resultando em perdas de energia na forma de calor. Esse aquecimento pode comprometer o desempenho de componentes eletromecânicos, como motores e transformadores, levando a falhas operacionais e até mesmo a danos permanentes. Para mitigar esse problema, é crucial realizar um projeto adequado e considerar a escolha de materiais que possuam uma baixa suscetibilidade a correntes parasitas. Além disso, o uso de dissipadores de calor e sistemas de resfriamento pode ajudar a controlar as temperaturas geradas.
Outro desafio importante é a detecção e a medição das correntes parasitas. Uma vez que essas correntes não são facilmente detectáveis, é vital implementar métodos de monitoramento que possibilitem a identificação de problemas antes que se tornem críticos. Técnicas de ensaio não destrutivo, como ultrassom e ensaios magnéticos, podem ser muito úteis nesse contexto. No entanto, o desenvolvimento de sistemas de medição eficazes e a formação de profissionais capacitados para realizar essas avaliações contínuas são aspectos que muitas vezes representam um desafio significativo para as empresas.
A complexidade dos sistemas elétricos também pode dificultar a interpretação dos dados relacionados às correntes parasitas. A presença de múltiplas variáveis, como a geometria dos componentes e as condições operacionais, pode resultar em situações onde as correntes parasitas se manifestam de maneira não linear. Isso pode tornar a análise dos dados mais complicada, exigindo uma abordagem cuidadosa na coleta e interpretação das informações. O desenvolvimento de modelos computacionais que simulem o comportamento dessas correntes e que ajudem na previsão de seus efeitos pode ser uma maneira de superar este desafio.
Adicionalmente, as variações na frequência dos campos magnéticos também são uma preocupação importante. As correntes parasitas estão intimamente relacionadas à frequência com que o campo magnético é aplicado. Quando a frequência aumenta, a intensidade das correntes parasitas também tende a aumentar, resultando em maiores perdas de energia e aquecimento. Isso é particularmente relevante em aplicações que operam em altas frequências, como os dispositivos de energia magnética e em algumas configurações de sistemas de transmissão. A escolha de materiais apropriados que apresentem comportamentos desejáveis a diferentes frequências, aliados ao desenvolvimento de técnicas de controle, se torna essencial para mitigar esse problema.
Outro desafio enfrentado no uso de correntes parasitas é a necessidade de atender a regulamentações e normas específicas que garantam a segurança e a eficácia dos sistemas. Muitas indústrias estão sujeitas a padrões rigorosos de desempenho e segurança, o que exige que as empresas implementem medidas eficazes de controle e análise de correntes parasitas. A conformidade contínua com essas normas pode representar uma carga adicional para os fabricantes e prestadores de serviços, que precisam investir em tecnologias de monitoramento e profissionais qualificados para garantir que as operações permaneçam dentro dos critérios estabelecidos.
Além disso, a integração de tecnologias emergentes, como a Internet das Coisas (IoT) e a inteligência artificial, também apresenta desafios. Embora essas tecnologias possam aumentar a eficácia dos sistemas de monitoramento de correntes parasitas, a implementação e a manutenção de soluções tecnológicas podem exigir investimentos significativos e a superação de barreiras técnicas. É fundamental que as empresas estejam preparadas para adotar essas inovações, capacitando sua equipe e garantindo que a infraestrutura adequada esteja em vigor para suportar a nova tecnologia sem comprometer a qualidade das operações existentes.
A complexidade do design dos produtos também deve ser considerada ao se trabalhar com correntes parasitas. Em muitas aplicações, o design dos componentes pode ser complicado e preciso, fazendo com que o gerenciamento das correntes parasitas torne-se um fator crítico a ser considerado durante a fase de projeto. Engenheiros de design e projetistas têm o dever de trabalhar em conjunto para criar soluções que minimizem as correntes parasitas, mantendo ao mesmo tempo a funcionalidade e a eficiência do produto final.
Finalmente, o custo associado ao controle e mitigação das correntes parasitas pode ser um desafio significativo para muitas empresas. A implementação de métodos adequados de monitoramento e análise pode exigir investimentos altos em equipamentos e treinamento. Portanto, as empresas precisam equilibrar os custos de gestão com os benefícios que as soluções oferecem. Ter uma visão clara do retorno sobre o investimento pode ajudar as organizações a justificar esses gastos e implementar as melhores soluções para suas necessidades específicas.
Em resumo, embora o uso de correntes parasitas pode trazer benefícios, é importante que as empresas reconheçam e enfrentem os desafios associados a esse fenômeno. Desde o aquecimento excessivo e a dificuldade na detecção, até as preocupações de design e regulamentações, as organizações devem adotar uma abordagem proativa, utilizando técnicas de ensaio não destrutivo e estratégias de mitigação eficazes para garantir a integridade e o desempenho dos seus sistemas. Com um planejamento cuidadoso e a adoção de tecnologias apropriadas, as empresas podem superar esses desafios e otimizar o uso das correntes parasitas nas suas operações.
Normas e regulamentações relacionadas
A segurança e a qualidade dos produtos e serviços em diversas indústrias são asseguradas por meio de normas e regulamentações. No contexto dos ensaios não destrutivos e da avaliação de correntes parasitas, a conformidade com essas normas é crucial para garantir a integridade dos materiais, a segurança operacional e a proteção ao meio ambiente. Neste artigo, vamos explorar algumas das principais normas e regulamentações relacionadas aos ensaios não destrutivos e ao monitoramento de correntes parasitas em várias indústrias.
Uma das mais conhecidas e amplamente adotadas normas na área de ensaios não destrutivos é a ASTM E1444, desenvolvida pela American Society for Testing and Materials (ASTM). Essa norma fornece diretrizes para a realização de ensaios não destrutivos por meio de métodos de líquido penetrante e magnético. A conformidade com a ASTM E1444 é essencial para garantir que os procedimentos de inspeção estejam alinhados com as melhores práticas internacionais, permitindo que os profissionais emitam relatórios consistentes e confiáveis sobre a integridade dos materiais testados.
Outra norma importante a ser considerada é a ASME B31.1, que trata do projeto e construção de sistemas de tubulação para usinas de energia e instalações industriais. Essa norma abrange requisitos de ensaio não destrutivo, assegurando que a integridade das tubulações seja avaliada adequadamente. Essas diretrizes são particularmente cruciais na prevenção de vazamentos e falhas catastróficas em sistemas críticos, como os de transporte de fluidos e gases.
Além das normas específicas, existem regulamentos que abrangem as questões de segurança no trabalho e a saúde ocupacional, como a norma ISO 45001. Esta norma internacional estabelece diretrizes para um sistema de gestão de segurança e saúde ocupacional, promovendo a conscientização sobre os riscos associados ao trabalho. Quando se trata de ensaios não destrutivos, é imperativo garantir que as práticas de inspeção não coloquem em risco a segurança dos operadores. A conformidade com a ISO 45001 contribui para a criação de um ambiente de trabalho seguro e eficaz, o que é fundamental em indústrias como a construção civil e a petroquímica.
A norma ISO 9001, que se refere ao sistema de gestão da qualidade, também é relevante no contexto de ensaios não destrutivos e correntes parasitas. A aplicação dessa norma garante que as organizações tenham processos estabelecidos para monitorar e avaliar a qualidade de seus produtos e serviços. A ISO 9001 exige que as empresas realizem inspeções e testes de maneira sistemática, o que inclui a implementação de ensaios não destrutivos em várias etapas do processo produtivo. Dessa forma, atende-se à necessidade deaceitar e cumprir os padrões de qualidade contínuos que garantem a satisfação do cliente.
As regulamentações específicas de setores, como a norma API 570, também são fundamentais. Desenvolvida pela American Petroleum Institute (API), essa norma fornece diretrizes para a inspeção, manutenção e reparo de dutos e sistemas de tubulação utilizados na indústria de petróleo e gás. Ela inclui a exigência de ensaios não destrutivos para a avaliação de integridade de materiais, assegurando que a operação de dutos e tanques não apresentem riscos de vazamento que possam ameaçar o meio ambiente ou a saúde pública.
No contexto internacional, a regulamentação NDT (Non-Destructive Testing) ISO/IEC 17025 é importante, pois refere-se aos requisitos gerais para a competência de laboratórios de ensaio e calibração. Essa norma aborda a necessidade de garantir que qualquer ensaio realizado, incluindo ensaios não destrutivos, ocorra em condições controladas e com equipamentos calibrados, assegurando resultados precisos e confiáveis. Laboratórios que buscam a acreditação ISO/IEC 17025 são obrigados a implementar processos rigorosos de controle de qualidade e gerenciamento de resultados.
Além disso, diversos países têm suas próprias normativas e diretrizes relacionadas a ensaios não destrutivos. Por exemplo, no Brasil, existem as Normas da Associação Brasileira de Normas Técnicas (ABNT), que estabelecem requisitos para a realização de ensaios não destrutivos. A norma NBR 14667 trata das diretrizes gerais para o setor de inspeção e ensaios não destrutivos, promovendo a padronização e a qualidade nos métodos de inspeção utilizados no país.
Com o avanço da tecnologia, as regulamentações e normas estão constantemente sendo atualizadas para se adaptarem às novas práticas e inovações. As empresas devem manter-se atentas a esses desenvolvimentos, pois a não conformidade com as normas pode resultar em sanções legais, perda de licenças operacionais ou danos à reputação. Portanto, a formação contínua e o acompanhamento das atualizações normativas são essenciais para os profissionais e organizações que atuam nos campos de ensaios não destrutivos e na avaliação de correntes parasitas.
Além das normas técnicas, é importante mencionar que a responsabilidade ambiental também está sendo incorporada nas regulamentações. Muitas indústrias estão sob a obrigação de reduzir seu impacto ambiental e garantir práticas de operação sustentáveis. Isso significa que as normas de ensaio não destrutivo e o monitoramento de correntes parasitas devem levar em conta a responsabilidade ambiental e social, atendendo às expectativas de sustentabilidade da sociedade atual.
Em resumo, as normas e regulamentações relacionadas aos ensaios não destrutivos e corredores parasitas desempenham um papel crucial na garantia da qualidade, segurança e integridade das operações industriais. A conformidade com essas diretrizes assegura que os processos estejam alinhados com as melhores práticas globais, protegendo não apenas as operações, mas também a saúde e a segurança das pessoas e o meio ambiente. Portanto, é fundamental que as organizações mantenham-se informadas e atualizadas em relação a essas normas a fim de garantir o sucesso operacional e a conformidade legal.
Em conclusão, o ensaio não destrutivo em correntes parasitas é uma ferramenta vital para a avaliação da integridade de materiais e a segurança de operações em diversas indústrias. A capacidade de detectar falhas internas sem danificar os componentes é essencial para a manutenção da eficiência e a prevenção de acidentes. Ao longo deste artigo, ficou evidente a importância dos ensaios não destrutivos e como eles podem ser aplicados em diferentes contextos para beneficiar as organizações. A adoção dessas práticas não só melhora a segurança operacional, mas também contribui para a sustentabilidade e a economia de custos a longo prazo. Portanto, investir em ensaios não destrutivos é fundamental para garantir a qualidade e a segurança dos produtos e sistemas, reforçando o compromisso das empresas com a excelência e a integridade em suas operações.