Ensaios mecânicos de materiais metálicos essenciais
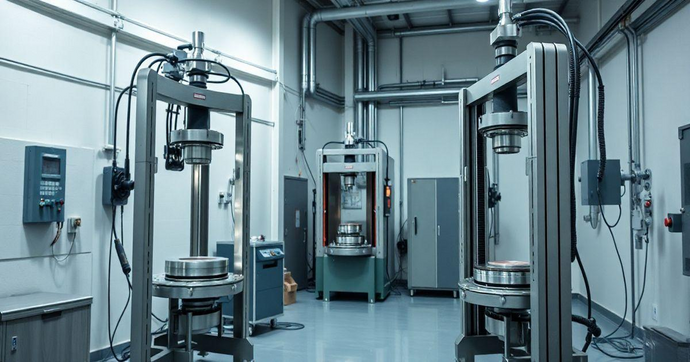
Por: João - 30 de Dezembro de 2024
Ensaios mecânicos materiais metálicos são fundamentais para determinar propriedades físicas e mecânicas de metais, essenciais na engenharia e na indústria. Neste artigo, abordaremos a importância desses ensaios, os métodos disponíveis e suas aplicações práticas. Se você deseja entender melhor como esses testes garantem a segurança e a eficiência dos produtos metálicos, continue lendo e descubra mais sobre o assunto.
Importância dos ensaios mecânicos na engenharia
Os ensaios mecânicos são uma parte crucial do processo de desenvolvimento e teste de materiais na engenharia. Eles permitem que os engenheiros compreendam como os materiais se comportam sob diferentes condições de carga, temperatura e ambiente. Esta compreensão é vital para garantir que os produtos finais sejam seguros, eficientes e de alta performance.
A importância dos ensaios mecânicos na engenharia se destaca em várias áreas, desde a construção civil até a indústria automotiva e aeroespacial. Nos projetos estruturais, por exemplo, é fundamental conhecer a resistência e a ductilidade dos materiais utilizados nas construções. Ensaios como tração, compressão e flexão são recursos valiosos para determinar se os materiais atenderão aos requisitos de segurança e funcionalidade em situações reais.
Além disso, esses ensaios ajudam na seleção de materiais. Com uma ampla gama de opções disponíveis, os engenheiros precisam saber quais materiais são mais adequados para aplicações específicas. Ensaios mecânicos fornecem dados quantitativos que apoiam a escolha de um material em detrimento de outro, levando em consideração não apenas a resistência mecânica, mas também a durabilidade, a resistência à corrosão e outros fatores cruciais.
Outro aspecto importante é a verificação de qualidade. Os ensaios mecânicos garantem que os materiais utilizados na fabricação de produtos atendam às especificações descritas nos documentos de engenharia. Isso é particularmente vital para indústrias que devem cumprir normas rigorosas, como a fabricação de componentes para a indústria aeroespacial. A falha de um único componente pode ter consequências catastróficas, e os ensaios mecânicos estabelecem uma linha de defesa contra tais riscos.
Além dos aspectos de segurança e qualidade, os ensaios mecânicos também influenciam o custo e a eficiência do processo de produção. Ao determinar as propriedades dos materiais, os engenheiros podem evitar o uso de materiais excessivamente caros que não oferecem vantagens significativas em relação aos mais econômicos. Isso resulta não apenas em redução de custos, mas também em um processo de produção mais eficiente.
A realização de ensaios mecânicos também permite que os engenheiros realizem análises de falhas. Quando um componente falha, a investigação das causas é essencial para evitar a repetição do acidente. Os ensaios mecânicos podem ser usados para simular as condições nas quais a falha ocorreu, permitindo que os engenheiros identifiquem problemas de design, fabricação ou material. A partir daí, medidas corretivas podem ser implementadas, resultando em produtos mais confiáveis e resilientemente projetados.
A tecnologia dos ensaios mecânicos tem evoluído significativamente nos últimos anos. Novas técnicas, como Ultrassom phased array, possibilitam a avaliação mais detalhada e precisa das propriedades dos materiais. Estas tecnologias permitem diagnósticos mais rápidos e efetivos da qualidade dos produtos e podem ajudar a otimizar processos de fabricação.
Por fim, vale ressaltar que o alinhamento entre as inovações tecnológicas e os ensaios mecânicos resultará na produção de materiais ainda mais robustos, flexíveis e eficientes. A engenharia está sempre em busca da excelência, e os ensaios mecânicos são uma ferramenta poderosa para alcançar esse objetivo.
Em suma, os ensaios mecânicos são indispensáveis na engenharia, desempenhando um papel vital na escolha de materiais, verificação de qualidade, análise de falhas e otimização de processos. À medida que a tecnologia avança, a capacidade de testar e compreender o comportamento dos materiais também se expande, permitindo que os engenheiros projetem soluções ainda mais inovadoras e seguras.
Tipos de ensaios mecânicos para materiais metálicos
Os ensaios mecânicos para materiais metálicos são clássicos na análise e avaliação das propriedades desses materiais. Os engenheiros utilizam diversos métodos para medir características como resistência, dureza, ductilidade e tenacidade, que são essenciais para assegurar que os metais atendam a padrões e requisitos específicos em aplicações industriais. Neste artigo, discutiremos os principais tipos de ensaios mecânicos, suas metodologias e a importância de cada um.
Os ensaios de tração são um dos tipos mais comuns de ensaios mecânicos realizados em materiais metálicos. Este teste envolve a aplicação de uma carga axial à amostra até que ocorra a ruptura. O resultado é uma curva tensão-deformação, que fornece informações valiosas sobre a resistência ao cisalhamento, o limite de escoamento e a percentagem de elongação. Esses dados são cruciais para entender como um metal se comporta sob diferentes condições de carga e são frequentemente utilizados na seleção de materiais para estruturas e componentes.
Outro tipo importante de ensaio mecânico é o ensaio de compressão. Neste método, a amostra é submetida a uma força compressiva, visando avaliar a resistência dos materiais à deformação quando submetidos a carga axial oposta. Esse ensaio é especialmente relevante para materiais que podem ser mais suscetíveis a falhas sob compressão, como alguns tipos de ligas metálicas. A compreensão do comportamento sob compressão ajuda os engenheiros a prever como os materiais se comportarão em aplicações práticas.
Os ensaios de dureza são usados para determinar a resistência de um material à impressão de um corpo duro, que é um indicativo da durabilidade e resistência ao desgaste. Os métodos de teste de dureza mais comuns incluem o teste Rockwell, Brinell e Vickers. Cada método utiliza diferentes forças e tamanhos de indentadores, proporcionando uma série de dados que ajudam a caracterizar a dureza do material. A dureza é um parâmetro essencial em muitas indústrias, como a automotiva e a fabricação de ferramentas.
Os ensaios de fadiga, por sua vez, atendem a uma necessidade crítica: a avaliação do desempenho dos materiais sob condições de carregamento cíclico. Esses testes são fundamentais para componentes que enfrentam variações repetitivas de tensão durante a operação, como rodas de aeronaves, peças de máquinas e estruturas de pontes. Implementando ciclos de tensão, é possível determinar a vida útil do material antes que a falha ocorra. Assim, os ensaios de fadiga reforçam a importância da durabilidade e da confiabilidade dos produtos.
Além dos ensaios mencionados, os testes de impacto também desempenham um papel vital na análise de materiais metálicos. Os ensaios de impacto, como o Ensaio Charpy, medem a resistência de um material a falhas repentinas, como cortes ou fraturas. É crucial para aplicações onde a segurança é primordial, como numa construção de edifícios e na criação de infraestruturas de transporte. Materiais que apresentam alta resistência ao impacto são essenciais em situações que envolvem choques e cargas dinâmicas.
Os ensaios de torção são outro tipo que não pode ser ignorado. Eles envolvem a aplicação de momentos torcionais em uma amostra e ajudam na avaliação de propriedades como a resistência ao cisalhamento e a rigidez. Esses ensaios se tornam particularmente relevantes em aplicações onde os componentes são sujeitos a forças de torção, como eixos de transmissão e suportes de estruturas rotativas.
Uma outra modalidade de ensaio que merece destaque é o ensaio visual de soldagem, que permite examinar e identificar falhas na estrutura de juntas soldadas através da observação. Embora não seja um ensaio mecânico tradicional, é essencial para garantir a integridade das soldas, que são frequentemente pontos críticos em estruturas metálicas. A visualização cuidadosa pode ajudar a detectar problemas antes que eles causem falhas catastróficas.
Por fim, a escolha do tipo de ensaio mecânico a ser realizado depende do material específico em questão, das exigências do projeto e da aplicação final. Cada teste tem suas próprias metodologias, vantagens e limitações. Portanto, ao projetar um novo produto ou ao avaliar um material existente, é essencial considerar a gama de ensaios mecânicos disponíveis. Isso garantirá que as propriedades dos materiais sejam totalmente compreendidas e que o objetivo final atenda às expectativas de desempenho, segurança e eficiência.
Em suma, os ensaios mecânicos são cruciais para a engenharia de materiais metálicos. Esses testes fornecem informações valiosas sobre as propriedades mecânicas, segurança e eficiência dos materiais, permitindo que os engenheiros façam escolhas informadas e assegurem a qualidade em suas aplicações.
Preparação de amostras para ensaios mecânicos
A preparação de amostras para ensaios mecânicos é um etapa fundamental que influencia diretamente a precisão e a confiabilidade dos resultados obtidos durante os testes. A forma como as amostras são preparadas pode afetar não apenas a medição das propriedades mecânicas, mas também a validade dos resultados e sua interpretação. Por isso, é essencial seguir um processo rigoroso e bem definido para garantir que as amostras representem com precisão os materiais a serem testados.
A primeira consideração na preparação de amostras é a escolha do material. Diferentes metais e ligas requerem técnicas específicas, e cada tipo de ensaio pode ter suas próprias necessidades particulares. Por exemplo, a geometria da amostra a ser utilizada em um ensaio de tração deve ser padronizada para garantir resultados consistentes. A norma ASTM E8, por exemplo, especifica as dimensões e a forma das amostras para ensaios de tração de metais. Seguir essas diretrizes é crucial para assegurar a comparabilidade dos resultados.
Depois da escolha do material e da definição das dimensões, o próximo passo na preparação é a usinagem da amostra. Este processo envolve técnicas como corte, fresagem ou torneamento, que moldam o material na forma necessária para o ensaio desejado. Durante a usinagem, é importante minimizar as alterações na estrutura interna do material, uma vez que isso pode introduzir tensões adicionais que afetarão as propriedades mecânicas. Por isso, muitos laboratórios optam por utilizar técnicas de usinagem a frio, evitando o aquecimento excessivo que pode alterar as propriedades do metal.
Além da usinagem, a limpeza da amostra é um aspecto vital que não pode ser negligenciado. As impurezas, como óleos, graxas ou partículas de sujeira, podem interferir nos resultados do ensaio, levando a leituras enganosas. Por isso, após o processo de usinagem, as amostras devem ser submetidas a um processo de limpeza cuidadoso, que pode incluir solventes específicos ou limpeza ultrassônica. A limpeza não apenas protege a integridade do teste, mas também assegura que o comportamento da amostra sob carga seja avaliado de forma precisa.
Durante a preparação, outro ponto a ser considerado é o tratamento superficial da amostra. Em alguns casos, pode ser necessário aplicar tratamentos térmicos ou tratamentos de superfície, que podem alterar as propriedades mecânicas da amostra. Por exemplo, um tratamento de têmpera pode aumentar a dureza de um aço, enquanto um revenimento pode melhorar sua tenacidade. Portanto, os engenheiros devem considerar como o tratamento afetará as propriedades gerais do material antes de realizar os ensaios.
A preparação de amostras também deve incluir a documentação detalhada de todas as etapas do processo. Isso envolve registrar as condições de usinagem, os métodos de limpeza e quaisquer tratamentos aplicados. Um rastreamento cuidadoso é crucial para garantir que todos os aspectos do teste sejam replicáveis e transparentes. Um bom registro pode ser vital em um ambiente de pesquisa ou produção, onde a repetibilidade dos testes é crítica para a validação dos resultados.
Uma vez que as amostras estão preparadas, é necessário etiquetá-las e armazená-las corretamente até o momento do ensaio. A forma como as amostras são armazenadas pode impactar suas propriedades, principalmente se forem expostas a ambientes corrosivos ou condições extremas. Portanto, o armazenamento deve ser feito em um ambiente controlado, onde fatores como temperatura, umidade e contaminação possam ser monitorados.
Os métodos de ensaios, sejam eles ensaios destrutivos ou não destrutivos, também condicionam a preparação das amostras. Nos ensaios destrutivos, como o ensaio de tração, a amostra geralmente é quebrada para se obter os dados, enquanto nos ensaios não destrutivos, é necessário garantir que não haja danos permanentes no material. Essa diferença significa que as considerações sobre a preparação da amostra podem variar de acordo com os métodos de ensaio escolhidos.
Finalmente, a comunicação entre o equipe de laboratório e os engenheiros é essencial. A preparação de amostras deve ser feita em um diálogo constante entre essas duas partes para garantir que todas as especificações e requisitos sejam atendidos. Um erro na preparação pode resultar em testes falhos e, consequentemente, em decisões baseadas em dados imprecisos, o que pode ter um impacto significativo em projetos e aplicações práticas.
Em resumo, a preparação de amostras para ensaios mecânicos é uma etapa crítica que requer atenção aos detalhes e prática meticulosa. Cada fase, desde a usinagem até o armazenamento, desempenha um papel crucial na qualidade dos resultados finais. A compreensão das melhores práticas para a preparação de amostras contribui não apenas para a precisão dos dados, mas também para a segurança e a eficácia dos produtos desenvolvidos na engenharia moderna.
Métodos de ensaio de tração em metais
Os métodos de ensaio de tração em metais são fundamentais para a avaliação das propriedades mecânicas desses materiais. Através desses ensaios, é possível determinar características cruciais, como limite de resistência, limite de escoamento, elongação e módulo de elasticidade. Esses dados são indispensáveis em diversas áreas da engenharia, abrangendo desde a construção civil até a indústria automotiva e aeroespacial. Neste artigo, vamos explorar os principais métodos de ensaio de tração em metais, suas aplicações e a importância de cada um.
Um dos métodos mais comuns para avaliar a resistência à tração em metais é o Ensaio de tração, que envolve a aplicação de uma carga uniaxial a uma amostra metálica até que ocorra a ruptura. O ensaio é projetado para medir a resposta do material à tensão aplicada, permitindo que os engenheiros analisem o comportamento do metal sob condições específicas. Este teste é crucial para a seleção de materiais para componentes estruturais, pois fornece informações sobre como o material se comportará em condições reais de operação.
O ensaio de tração normalmente é realizado em uma máquina de ensaio de tração, que é equipada com dispositivos para aplicar, medir e controlar a força. A amostra, que deve ser cuidadosamente preparada, é posicionada entre duas garras que a seguram firmemente. À medida que a força é aplicada, a elongação da amostra e a carga são monitoradas em tempo real. O resultado desse teste é uma curva tensão-deformação, que fornece um perfil completo do comportamento do material até a ruptura.
Os testes geralmente seguem padrões e normas reconhecidos, como a ASTM E8, que especifica as diretrizes para a execução do ensaio, incluindo as dimensões da amostra e as condições de teste. A padronização é fundamental para garantir a reprodutibilidade e a confiança dos resultados obtidos. A precisão no preparo das amostras é vital, pois qualquer imperfeição ou variação nas dimensões pode resultar em medições incorretas.
Nos ensaios de tração, a interpretação dos resultados é igualmente importante. A curva tensão-deformação obtida fornece uma visualização clara do comportamento do material. Inicialmente, a curva apresenta uma região linear, que representa o limite elástico, onde o material se comporta de acordo com a Lei de Hooke. Após essa fase, a curva começa a exibir uma deformação plástica, indicando que o material começa a se deformar permanentemente sob carga.
O ponto em que a curva atinge seu máximo é conhecido como limite de resistência à tração, o qual indica a maior tensão que o material pode suportar antes de falhar. O limite de escoamento, por outro lado, é a tensão em que o material começa a se deformar plasticamente. Ambos os valores são críticos para a análise de segurança em projetos de engenharia, pois ajudam a determinar a capacidade de carga do material.
Além do ensaio de tração convencional, existem outros métodos de ensaio que podem ser utilizados para analisar materiais sob tensão. Um desses métodos é o ensaio de tração em altas temperaturas, que é realizado para avaliar o comportamento de metais quando submetidos a condições térmicas extremas. Esse tipo de teste é especialmente relevante em setores como o da energia, onde materiais permanecem expostos a altas temperaturas durante longos períodos.
Outra opção é o teste de tração em condições de fadiga. Nesse caso, são aplicadas tensões cíclicas à amostra para simular o ambiente de operação real em que o componente estará inserido. Os ensaios de fadiga são fundamentais para entender a durabilidade e a resistência do material a falhas quando submetido a ciclos repetidos de carga, como em estruturas de aeronaves ou componentes de máquinas pesadas.
Os métodos modernos de ensaio de tração também incorporam tecnologias avançadas, como o uso de extensômetros ópticos, que permitem medições de deformação sem contato. Esses dispositivos oferecem maior precisão e a possibilidade de monitorar deformações em tempo real durante a aplicação da carga, fornecendo dados mais detalhados sobre o comportamento do material sob tensão.
Além disso, a análise de fraturas após os ensaios de tração oferece informações valiosas sobre os modos de falha dos metais. A observação da fratura pode revelar características que indicam se a falha ocorreu devido a tensões excessivas, desgaste por fadiga ou outros fatores. Esse tipo de análise é crucial para aprimorar o projeto de materiais e componentes, aumentando sua confiabilidade e segurança.
Em conclusão, os métodos de ensaio de tração em metais são essenciais para a caracterização e análise do comportamento mecânico de materiais. Estes ensaios fornecem informações importantes que têm impacto direto na seleção de materiais para aplicações industriais e na segurança de projetos de engenharia. Com a evolução das tecnologias de teste, os engenheiros têm à disposição ferramentas cada vez mais avançadas para garantir que os produtos atendam aos mais altos padrões de qualidade e segurança.
Teste de dureza: o que é e como é realizado
O teste de dureza é uma das metodologias mais reconhecidas e utilizadas na avaliação de materiais metálicos. Este procedimento visa medir a resistência de um material à deformação plástica, que é um indicativo de sua durabilidade e desempenho sob condições de uso. A dureza é uma propriedade fundamental, especialmente em aplicações onde o desgaste e a abrasão estão presentes, como na fabricação de ferramentas, componentes automotivos e estruturas metálicas. Neste artigo, discutiremos o que é o teste de dureza, os métodos utilizados e como ele é realizado.
A dureza é definida como a capacidade de um material resistir à penetração de um corpo duro. Esse conceito é fundamental na indústria, pois materiais com alta dureza tendem a ter melhor resistência ao desgaste, enquanto materiais com baixa dureza podem ser mais suscetíveis a danos e deformações. A medição da dureza pode ser feita de diferentes formas, utilizando métodos que variam de acordo com as características do material a ser testado e a aplicação desejada.
Existem vários métodos de teste de dureza, sendo os mais comuns o teste Rockwell, o teste Brinell e o teste Vickers. Cada um deles possui características e aplicações distintas, adequadas para diferentes tipos de materiais e exigências de precisão.
O teste Rockwell, por exemplo, utiliza uma carga menor para realizar a medição da dureza de materiais, proporcionando resultados rápidos e eficientes. Este método aplica um indentador, que pode ser uma esfera de aço ou um disco de diamante, na superfície do material, e depois aplica uma carga adicional. A dureza Rockwell é expressa em uma escala que varia dependendo do indentador utilizado e da carga aplicada. As escalas mais comuns incluem HRA, HRB e HRC, cada uma adequada para diferentes tipos de materiais.
Em contrapartida, o teste Brinell é ideal para materiais mais macios e é amplamente utilizado em aços e fundições. Neste método, uma esfera de aço endurecido é aplicada com uma carga na superfície do material. Após o teste, a profundidade da impressão deixada na superfície é medida, permitindo calcular a dureza Brinell. Este método é especialmente útil para avaliar materiais que possuem microestruturas variadas, pois fornece uma média da dureza ao longo de uma área maior.
O teste Vickers, por sua vez, se destaca pela versatilidade e precisão. Utilizando um indentador de diamante piramidal, este teste pode ser aplicado a uma ampla gama de materiais, desde metais até cerâmicas. A dureza Vickers é calculada medindo-se a diagonal da impressão deixada pelo indentador e é expressa em termos de HV (dureza Vickers). Este método é particularmente valioso em aplicações onde a precisão dos dados é fundamental, como na pesquisa e desenvolvimento de novos materiais.
A realização do teste de dureza envolve um procedimento padronizado, que assegura que os resultados sejam consistentes e confiáveis. Primeiramente, a amostra deve ser devidamente preparada, o que frequentemente inclui o polimento da superfície para eliminar imperfeições que poderiam afetar a medição. A preparação da amostra é crucial, pois qualquer alteração na superfície, como riscos ou sujeira, pode comprometer os resultados do teste.
Uma vez que a amostra está pronta, ela é posicionada na máquina de teste de dureza. Dependendo do método escolhido, a máquina aplicará uma carga específica sobre o indentador. Após um período predeterminado, a carga é removida, e a profundidade ou a área da impressão deixada na amostra é medida. Essa medida é crucial para determinar a dureza do material.
Após a execução do teste, os dados obtidos devem ser analisados e documentados. Os resultados são geralmente expressos em uma unidade de dureza específica, sendo fundamental que esses dados sejam interpretados no contexto da aplicação pretendida. Por exemplo, um material que apresenta dureza elevada pode ser mais adequado para aplicações onde há atrito intenso, enquanto materiais com dureza mais baixa podem ser mais adequados para aplicações que exigem maior ductilidade e resistência à deformação.
Os testes de dureza são amplamente utilizados em várias indústrias. Na fabricação de ferramentas, por exemplo, é essencial garantir que as lâminas e cortes tenham dureza suficiente para resistir ao desgaste. Na indústria automotiva, os componentes como eixos e engrenagens precisam ter características específicas de dureza para garantir o funcionamento eficiente e seguro dos veículos. Além disso, em setores como o de construção civil, a dureza dos materiais metálicos que compõem estruturas e fundações também é uma consideração crítica.
Em resumo, o teste de dureza é uma ferramenta vital na avaliação de materiais metálicos, proporcionando informações cruciais sobre suas propriedades e desempenho. Seus vários métodos, incluindo Rockwell, Brinell e Vickers, oferecem flexibilidade e adaptabilidade a diferentes situações e requisitos. A realização cuidadosa deste teste e a interpretação dos resultados são essenciais para garantir a qualidade e a segurança dos produtos finais utilizados em uma variedade de indústrias.
Fatigue testing: avaliando a resistência ao desgaste
O fatigue testing, ou teste de fadiga, é uma metodologia essencial na avaliação da resistência de materiais mecânicos ao desgaste e à falha sob condições de carga cíclica. As aplicações desse tipo de teste se estendem por diversas indústrias, incluindo a automotiva, aeroespacial e de geração de energia, onde componentes estão sujeitos a repetidos ciclos de estresse durante seu funcionamento. Este artigo irá explorar o conceito de teste de fadiga, seus métodos aplicáveis e a importância da avaliação da resistência ao desgaste em materiais metálicos.
A fadiga é um fenômeno que se refere à degradação de um material após múltiplas variações de carga que, mesmo sendo inferiores ao seu limite de resistência, podem levar à falha. A falha por fadiga geralmente não é uma ocorrência imediata, mas sim um processo que se desenvolve ao longo do tempo, dificultando a previsão de quando e onde um componente pode falhar. É por isso que o fatigue testing é uma ferramenta crítica para os engenheiros, permitindo que eles anticipem o comportamento do material sob condições normais de uso.
O teste de fadiga pode ser realizado de diversas maneiras, dependendo das especificidades da aplicação e do material a ser avaliado. Um dos métodos mais comuns é o ensaio de fadiga em tensão alternada, em que uma amostra é submetida a ciclos de estresse que alternam entre tensões positivas e negativas. Esse método é particularmente relevante para estruturas que, na prática, estão frequentemente sujeitas a cargas variáveis, como as que ocorrem em aeronaves e veículos.
Nos ensaios de fadiga, a amostra é segurada em uma máquina de teste que aplica e controla as forças envolvidas. Durante o experimento, a amostra é submetida a uma série de taxas de estresse e número de ciclos pré-definidos, enquanto são registradas as deformações e tensões ocorridas. O número de ciclos que um material pode suportar antes de falhar é chamado de “vida à fadiga”, e esse parâmetro é crucial para a análise de segurança em projetos de engenharia.
Outro aspecto importante do teste de fadiga é a determinação do limite de fadiga, que é a tensão máxima que um material pode suportar indefinidamente sem falha. Isso é particularmente valioso em aplicações onde a segurança é de suma importância, como na construção de pontes e na fabricação de componentes para aeronaves. O conhecimento do limite de fadiga permite aos engenheiros projetar componentes que não só resistam às forças aplicadas, mas também que tenham uma vida útil confiável em condições variáveis de carga.
O teste de fadiga não se limita apenas à tensão alternada; também existem ensaios de fadiga rotacional e de fadiga por flexão, que estão relacionados a casos específicos de uso. O ensaio de fadiga rotacional é comumente utilizado em componentes cilíndricos, como eixos e engrenagens, enquanto o ensaio de fadiga por flexão é adequado para varetas e vigas. Cada um desses métodos fornece informações diferentes, permitindo que os engenheiros adaptem suas análises para atender às necessidades específicas de seus projetos.
Uma das vantagens do teste de fadiga é a capacidade de identificar ineficiências e pontos fracos nos materiais e estruturas. Ao examinar as características da falha após os testes, é possível entender como e por que um material falhou. Isso permite que os engenheiros aprimorem os materiais utilizados, desenvolvendo novas ligas com melhor resistência à fadiga ou ajustando as geometrias de componentes para evitar concentrações indesejadas de estresse.
Além de avaliar a resistência a falhas, o teste de fadiga também é importante na validação de processos de fabricação. Por exemplo, processos como soldagem e tratamento térmico podem alterar significativamente a microestrutura de um material, influenciando sua resistência a fadiga. Ao realizar testes de fadiga em amostras que passaram por diferentes processos de fabricação, os engenheiros podem determinar quais métodos produzem materiais mais duráveis e confiáveis.
Outro ponto relevante é a consideração de fatores ambientais, como temperatura, umidade e corrosão. As condições em que um componente será utilizado podem impactar diretamente sua resistência à fadiga. Portanto, é comum que os testes incluam variáveis ambientais para simular as condições reais de operação. Por exemplo, na indústria automotiva, os testes de fadiga podem simular as condições de uma estrada para avaliar como um veículo irá se comportar ao longo do tempo.
O fatigue testing se tornou uma prática padrão em engenharias contemporâneas, muito contribuído pelo avanço da tecnologia de testes. As máquinas de ensaio modernas são equipadas com sensores e sistemas de monitoramento que permitem a coleta de dados detalhados em tempo real, facilitando a análise e compreensão dos comportamentos dos materiais durante os ensaios.
Em suma, o teste de fadiga é uma ferramenta essencial para a avaliação da resistência ao desgaste e à degradação de materiais metálicos. Sua capacidade de simular condições reais de operação e avaliar o desempenho sob cargas cíclicas torna esse método crucial para garantir a segurança e confiabilidade de componentes em várias indústrias. A implementação de práticas eficazes de fatigue testing pode economizar tempo e recursos, evitando falhas catastróficas e proporcionando confiança na durabilidade dos materiais desenvolvidos.
Influência da temperatura nos ensaios mecânicos
A influência da temperatura nos ensaios mecânicos é um fator crítico que não pode ser ignorado ao caracterizar os materiais. A temperatura pode afetar drasticamente as propriedades mecânicas dos materiais, como resistência, ductilidade e dureza, além de influenciar suas respostas em condições de carga. Neste artigo, exploraremos como a temperatura impacta os ensaios mecânicos, as práticas adequadas para avaliar essas influências e a importância de considerar esse fator nas análises de materiais.
Os materiais, em função de sua estrutura cristalina e composição química, apresentam comportamentos distintos sob variações de temperatura. Em geral, a maioria dos metais torna-se mais maleável à medida que a temperatura aumenta, o que significa que eles podem se deformar mais facilmente sob tensão. Esta propriedade é crítica em aplicações onde os metais serão submetidos a altas temperaturas, como em caldeiras, motores e processos metalúrgicos. Assim, é essencial realizar ensaios mecânicos em condições que simulem o ambiente real de operação do material.
Um dos tipos de ensaio que mais sofre com o impacto da temperatura é o ensaio de tração. Ao elevar a temperatura, os limites de escoamento e de resistência à tração dos metais podem diminuir, resultando em um comportamento mais dúctil. Isso significa que, em temperaturas elevadas, um metal que geralmente é considerado rígido pode apresentar uma deformação plástica significativa antes de atingir o ponto de falha. Portanto, ao realizar ensaios de tração, especialmente em ligas metálicas, é fundamental considerar a temperatura para obter resultados representativos.
Por outro lado, a redução da temperatura costuma levar ao aumento da dureza e à diminuição da ductilidade. Materiais que estão em condições de frio extremo podem se comportar de maneira mais frágil, resultando em fraturas abruptas. Isso é extremamente importante em aplicações que envolvem ambientes frios, como na indústria do petróleo e gás, onde componentes são frequentemente expostos a temperaturas baixas. Os ensaios de dureza em temperaturas reduzidas podem revelar informações críticas sobre a tenacidade e a resistência à fratura dos materiais.
Ademais, a temperatura também pode afetar as características de resistência ao desgaste dos materiais, um aspecto fundamental que é analisado através dos testes de fadiga. À medida que a temperatura aumenta, a capacidade do material de resistir ao desgaste pode ser alterada, especialmente se ele estiver sujeito a tensões repetidas. O elevador de temperatura pode atuar como um moderador na resposta do material, resultando em uma diminuição do limite de fadiga em alguns casos. Isso destaca a importância de realizar testes de fadiga a diferentes temperaturas para entender a durabilidade e a confiabilidade dos componentes em operações reais.
Os testes de impacto, como o teste Charpy, também são influenciados pela temperatura. Um material a uma temperatura ambiente pode demonstrar um comportamento mais dúctil, enquanto a temperaturas mais baixas, pode revelar um comportamento mais frágil. Esse fenômeno é especialmente relevante em situações onde um material pode receber choques ou impactos, como em estruturas metálicas expostas a variações climáticas. Realizar esses testes em diferentes temperaturas pode ajudar engenheiros e projetistas a compreender melhor as propriedades de segurança dos materiais usados em construções ou na indústria automotiva.
Para que os ensaios mecânicos sejam precisos e representativos, é essencial que os laboratórios realizem testes sob condições controladas de temperatura. Isso inclui a utilização de câmaras climáticas que possam simular variações térmicas ao longo do ensaio. A calibração de equipamentos de ensaio também deve incluir considerações sobre a temperatura, assegurando que os resultados sejam consistentes e confiáveis. Em muitos casos, as normas internacionais, como ASTM e ISO, especificam a temperatura a ser mantida durante os ensaios, garantindo que os dados obtidos sejam válidos e comparáveis.
A interpretação dos resultados dos ensaios mecânicos também deve levar em conta as influências térmicas. Engenheiros e pesquisadores devem estar cientes de como o comportamento dos materiais variará com as mudanças de temperatura e como isso pode afetar as decisões de projeto e fabricação. Ao incluir dados sobre temperatura na análise de propriedades mecânicas, é possível desenvolver componentes que atendam aos requisitos de desempenho em suas condições de uso específicas.
Além disso, considerar a influência da temperatura nos ensaios mecânicos é fundamental para o desenvolvimento de novos materiais e ligas. À medida que a pesquisa avança em busca de materiais com propriedades superiores, a compreensão das interações térmicas se torna um elemento chave no processo de design e desenvolvimento. A manipulação da temperatura durante a fabricação pode ser utilizada como uma forma de otimizar as propriedades finais dos materiais, levando a produtos mais robustos e confiáveis.
Por fim, a influência da temperatura nos ensaios mecânicos é um fator determinante que não pode ser negligenciado. Compreender como a temperatura afeta as propriedades dos materiais permite que engenheiros e projetistas façam escolhas mais informadas, desenvolvam produtos mais seguros e eficientes e garantam que suas aplicações atendam aos padrões de segurança e qualidade exigidos na indústria moderna. Assim, a atenção à temperatura não é apenas uma questão técnica, mas uma prática essencial que pode impactar profundamente o desempenho e a vida útil dos materiais em uso.
Aplicações dos resultados dos ensaios mecânicos
Os ensaios mecânicos são fundamentais na engenharia e na ciência dos materiais, pois fornecem informações valiosas sobre as propriedades físicas e mecânicas de diversos materiais. A aplicação dos resultados obtidos desses ensaios é ampla e se estende a diferentes setores, desde a construção civil até a indústria automotiva e aeroespacial. Neste artigo, abordaremos algumas das principais aplicações dos resultados dos ensaios mecânicos e como eles influenciam o desenvolvimento e a segurança de produtos e estruturas.
Uma das principais aplicações dos resultados de ensaios mecânicos é a **seleção de materiais**. Ao entender as propriedades de um material, como resistência à tração, dureza e ductilidade, engenheiros e arquitetos podem escolher o material mais adequado para uma determinada aplicação. Por exemplo, ao projetar uma estrutura de suporte, como uma ponte ou um edifício, é crucial utilizar materiais que suportem as cargas esperadas e ofereçam resistência a fatores ambientais, como corrosão e fadiga. Os resultados dos ensaios ajudam a definir quais materiais são mais apropriados para suportar essas condições.
Além disso, a **análise de falhas** é outra aplicação significativa dos resultados dos ensaios mecânicos. Quando um componente falha, a investigação das causas da falha é essencial para o aprimoramento do design e da fabricação. Os ensaios mecânicos desempenham um papel vital nesse processo, permitindo que os engenheiros identifiquem as condições em que a falha ocorreu. Isso inclui determinar se a falha foi causada por fadiga, sobrecarga, ou defeitos de fabricação, como inclusão de impurezas no material. A partir daí, melhorias podem ser implementadas no material, no processo de fabricação ou no design do componente para evitar falhas similares no futuro.
Os ensaios mecânicos também são cruciais na **validação de processos de fabricação**. Por exemplo, processos como soldagem, forjamento e tratamento térmico podem alterar as propriedades mecânicas de um material. Realizar ensaios em materiais que passaram por esses processos ajuda a confirmar que os métodos utilizados produzem resultados que atendem aos padrões de qualidade e segurança. Essa validação é fundamental para indústrias que requerem altos níveis de precisão e confiabilidade, como a aeroespacial, onde o desempenho e a segurança são cruciais.
Em adição, a **previsão de desempenho** dos produtos também é uma aplicação importante. Os resultados dos ensaios mecânicos permitem que os engenheiros simulem o desempenho dos materiais sob diversas condições operacionais. Por exemplo, o teste de fadiga fornece informações sobre quantos ciclos de carga um componente pode suportar antes de falhar. Essa informação é vital para produtos que estão sujeitos a cargas cíclicas, como eixos de turbinas e sistemas de suspensão de veículos. Compreender a durabilidade esperada pode ajudar na programação de manutenções e substituições, assim como na otimização de designs para maior vida útil do produto.
Os resultados dos ensaios mecânicos também são aplicados para **garantir a conformidade com normas e regulamentações**. Muitas indústrias são regidas por normas rigorosas que especificam a necessidade de ensaios para garantir a segurança e a eficiência dos produtos. Por exemplo, na indústria automobilística, os testes de colisão e de resistência de materiais são realizados para garantir que os veículos atendam aos requisitos de segurança. Os resultados dos ensaios mecânicos são utilizados para comprovar que os produtos estão conformes, assegurando que eles possam ser comercializados e usados com segurança.
Neste contexto, os ensaios de dureza são frequentemente utilizados para determinar se materiais usados na fabricação de ferramentas e máquinas são capazes de suportar condições adversas e resistir ao desgaste. Os resultados desses testes são essenciais para a formulação de especificações e garantias de qualidade. Assim, as empresas podem oferecer produtos que não só atendem, mas superam as expectativas de desempenho e durabilidade.
As **inovações em materiais** também se beneficiam dos resultados de ensaios mecânicos. À medida que novos compósitos e ligas são desenvolvidos, a realização de ensaios mecânicos é necessária para entender suas propriedades e viabilidade para aplicações específicas. Isso se torna crucial em indústrias como a eletrônica, onde o desenvolvimento de novos materiais leves e resistentes pode levar a dispositivos mais eficientes e duráveis. O conhecimento obtido através de ensaios permite que os pesquisadores ajustem fórmulas e processos para otimizar as características dos novos materiais.
Por fim, a aplicação dos resultados de ensaios mecânicos é fundamental para o desenvolvimento de estratégias de **manutenção preditiva**. Ao avaliar o desempenho dos materiais ao longo do tempo e entender como suas propriedades mudam sob diferentes condições, as empresas podem implementar planos de manutenção que minimizam paradas indesejadas e aumentam a eficiência operacional. A capacidade de prever falhas potenciais economiza tempo e recursos, além de melhorar a segurança no ambiente de trabalho.
Em resumo, os resultados dos ensaios mecânicos são essenciais em uma ampla gama de aplicações, desde a seleção de materiais até a análise de falhas, validação de processos de fabricação, previsão de desempenho e conformidade com normas. Com o avanço das tecnologias e processos, a importância desses ensaios continua a crescer, proporcionando um papel crítico na segurança, eficiência e evolução dos produtos utilizados pela indústria moderna.
Em conclusão, os ensaios mecânicos de materiais metálicos desempenham um papel vital na engenharia e na indústria moderna. Eles são fundamentais para a compreensão das propriedades físicas e mecânicas dos metais, garantindo que os produtos atendam aos padrões de segurança e eficiência exigidos. Ao longo deste artigo, discutimos a importância dos ensaios, os diversos métodos disponíveis e as numerosas aplicações de seus resultados, que vão desde a seleção de materiais até a validação de processos de fabricação. Compreender esses aspectos é essencial para engenheiros, pesquisadores e profissionais envolvidos na criação e desenvolvimento de produtos metálicos. Assim, a realização rigorosa dos ensaios mecânicos não apenas aprimora a qualidade e a durabilidade dos materiais, mas também contribui para inovações que atendem às necessidades crescentes da sociedade e da indústria.