Ensaios Não Destrutivos END: Descubra Sua Importância e Aplicações
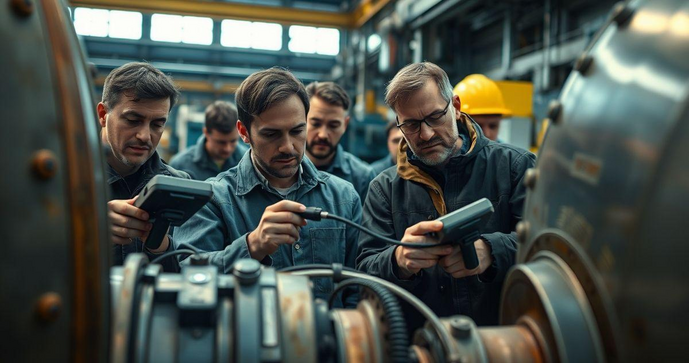
Por: João - 18 de Abril de 2025
O que são Ensaios Não Destrutivos e Seus Tipos
Os ensaios não destrutivos (END) são um conjunto de técnicas que permitem a avaliação da integridade de materiais e estruturas sem causarem danos.
Esses métodos são cruciais em diversos setores, pois permitem identificar falhas e desvios de qualidade sem comprometer a utilidade do item analisado.
Existem diversos tipos de END, cada um adequado a diferentes situações e materiais.
Entre os principais, destacam-se:
1. Radiografia Industrial: Utiliza radiação para detectar falhas internas em materiais.
É amplamente usada em soldagens e estruturas metálicas, permitindo visualizar detalhes que não são perceptíveis a olho nu.
2. Ultrassom: Usa ondas sonoras de alta frequência para investigar a espessura de materiais e detectar descontinuidades.
É um método eficaz tanto em metais quanto em compósitos.
3. Inspeção por Líquidos Penetrantes: Consiste na aplicação de um líquido que penetra em fissuras e descontinuidades.
Após a remoção do líquido, um produto revelador é aplicado, tornando as falhas visíveis.
4. Teste de Brinell e Rockwell: Estes são métodos de dureza que, apesar de não serem diretamente considerados END, são importantes para verificar as propriedades mecânicas dos materiais sem lhes causar danos significativos.
5. Termografia: Explora as diferenças de temperatura na superfície de um objeto.
Essa técnica é útil para identificar problemas térmicos em sistemas elétricos e mecânicos, sinalizando falhas potenciais.
Esses métodos não apenas contribuem para a segurança estrutural, mas também oferecem vantagens econômicas ao reduzir custos com manutenção e interrupções na produção.
A escolha do tipo de ensaio depende do material, da natureza das falhas a serem detectadas e do ambiente de trabalho.
Principais Vantagens dos Ensaios Não Destrutivos
Os ensaios não destrutivos (END) oferecem diversas vantagens significativas que tornam sua utilização essencial em várias indústrias. Entre os principais benefícios, destacam-se:
1. Preservação do Material: Como o próprio nome sugere, os ensaios não destrutivos possibilitam a avaliação de estruturas e componentes sem danificá-los. Isso garante que o item possa continuar a ser utilizado após a inspeção.
2. Detecção Precoce de Falhas: Os END permitem identificar falhas internas ou superficiais antes que se tornem problemas sérios. Essa detecção precoce pode evitar acidentes, garantido a segurança dos trabalhadores e a integridade das operações.
3. Economia de Tempo e Custos: As técnicas de END podem ser realizadas de forma rápida e eficiente, reduzindo o tempo de parada de equipamentos e processos. Isso se traduz em economia financeira, pois limita interrupções nas operações.
4. Aumento da Vida Útil dos Componentes: Ao identificar e corrigir falhas precoces, os END contribuem para prolongar a vida útil de máquinas e estruturas. Isso resulta em menos necessidade de substituições e reparos frequentes.
5. Versatilidade: Os diferentes tipos de ensaios não destrutivos podem ser aplicados a uma ampla gama de materiais e estruturas, incluindo metais, plásticos, compósitos e concreto. Essa versatilidade torna-os adaptáveis a diversas indústrias.
6. Regulamentação e Normatização: Muitos setores exigem a realização de ensaios não destrutivos como parte de normativas de segurança e qualidade. A conformidade com essas normas não apenas assegura a segurança, mas também promove a confiança do cliente.
Estas vantagens tornam os ensaios não destrutivos uma escolha inteligente e necessária para garantir a segurança e a eficiência nas operações industriais.
Aplicações de END na Indústria Aeronáutica
A indústria aeronáutica é uma das áreas onde os ensaios não destrutivos (END) desempenham um papel crucial. A segurança dos voos e a integridade das aeronaves dependem de rigorosos processos de verificação e avaliação. As aplicações de END nesta indústria incluem:
1. Inspeção de Estruturas Metálicas: Componentes como fuselagens, asas e suportes são submetidos a ensaios não destrutivos para detectar falhas internas e superficiais que possam comprometer a segurança da aeronave.
2. Verificação de Juntas Soldadas: As soldagens nos materiais das aeronaves são inspecionadas para identificar possíveis descontinuidades que possam afetar a performance estrutural. Métodos como radiografia e ultrassom são amplamente utilizados nessa aplicação.
3. Exame de Materiais Compósitos: Com a crescente utilização de compósitos na fabricação de aeronaves, ensaios não destrutivos como inspeção por ultrassom e termografia são utilizados para verificar a integridade desses materiais leves e resistentes.
4. Monitoramento de Componentes Críticos: Componentes como motores e sistemas hidráulicos precisam ser monitorados regularmente. Ensaios não destrutivos ajudam a identificar desgastes e falhas antes que afetem o desempenho operacional.
5. Inspeção de Aeronaves Alternadas e Inspeções Periódicas: As aeronaves devem passar por inspeções regulares de acordo com as normas da aviação civil. Os END são metodologias chave para garantir que as aeronaves cumpram os padrões necessários antes de cada voo.
6. Teste de Itens de Equipamento: Equipamentos de segurança, como cintos de segurança e sistemas de emergência, também são inspecionados usando técnicas NÃO destrutivas, assegurando que todos os sistemas estão operacionais e seguros para uso.
Essas aplicações são essenciais para manter a confiabilidade e segurança das aeronaves, minimizando riscos e garantindo um transporte aéreo seguro para passageiros e cargas.
Como Funciona a Radiografia Industrial em END
A radiografia industrial é uma das técnicas mais utilizadas dentro dos ensaios não destrutivos (END) e é essencial para a avaliação da integridade de componentes, especialmente em indústrias críticas como a aeronáutica, petroquímica e construção pesada. Este método utiliza radiação ionizante para gerar imagens que revelam a estrutura interna dos materiais.
1. Princípio de Funcionamento: A radiografia industrial funciona com a emissão de raios X ou raios gama que passam através do material a ser inspecionado. Quando esses raios atingem um filme fotográfico ou um detector digital, eles criam uma imagem que representa a densidade do material. Áreas mais densas e com menos vazios aparecem mais claras, enquanto áreas menos densas aparecem escuras.
2. Equipamentos Utilizados: Os principais equipamentos envolvidos na radiografia industrial incluem a fonte de radiação, que pode ser um tubo de raios X ou uma fonte radioativa, além de filmes radiográficos, placas digitais ou sistemas de imagem computorizada que capturam as imagens geradas.
3. Preparação da Amostra: Antes do ensaio, a amostra deve ser limpa e posicionada adequadamente. Qualquer contaminante, como óleo ou sujeira, pode afetar a qualidade da imagem radiográfica. A amostra é então colocada entre a fonte de radiação e a placa de captura.
4. Exposição e Desenvolvimento: A amostra é exposta à radiação por um período específico. Após a exposição, o filme é desenvolvido em um ambiente controlado, onde a imagem é revelada. No caso de sistemas digitais, a imagem é processada imediatamente.
5. Análise das Imagens: Um técnico qualificado analisa as imagens radiográficas em busca de descontinuidades, como trincas, porosidade ou inclusões não metálicas. Essa interpretação deve ser feita com base em normas e códigos de prática estabelecidos para garantir a segurança e eficácia da avaliação.
6. Interpretação e Relatório: Após a análise, um relatório detalhado é elaborado. Esse documento contém informações sobre a qualidade da solda ou do material avaliado, incluindo qualquer falha detectada e suas implicações para a segurança operacional.
A radiografia industrial é uma ferramenta poderosa que proporciona segurança e confiabilidade, identificando potenciais falhas antes que se tornem problemas graves. Sua capacidade de revelar defeitos invisíveis a olho nu é fundamental para a manutenção da qualidade em quase todos os segmentos industriais.
Métodos de Inspeção por Ultrassom: Uma Abordagem Eficaz
A inspeção por ultrassom é um método amplamente utilizado nos ensaios não destrutivos (END), permitindo a avaliação interna de materiais e estruturas de forma precisa e confiável. Este método é especialmente eficaz para detectar descontinuidades e medir espessura em uma variedade de materiais.
1. Princípio de Funcionamento: A técnica de ultrassom envolve a emissão de ondas sonoras de alta frequência, que são introduzidas no material a ser inspecionado através de um transdutor. Essas ondas viajam pelo material e, ao encontrar descontinuidades ou diferenças de densidade, são refletidas de volta ao transdutor, que as converte em sinais elétricos.
2. Equipamentos Utilizados: Os principais componentes de um sistema de inspeção por ultrassom incluem o gerador de ondas ultrassônicas, os transdutores, que podem ser do tipo de contato ou imersão, e um analisador, que traduz os sinais recebidos em imagens ou gráficos que representam a integridade do material.
3. Tipos de Inspeção por Ultrassom: Existem diferentes métodos dentro da inspeção por ultrassom, incluindo a técnica de pulso-eco, onde o tempo que leva para o eco retornar é medido, e a técnica de transmissão, onde o ultrassom é transmitido de um lado para o outro do material. Ambas são eficazes em detectar falhas como trincas, poros e corrosão.
4. Preparação e Execução: A preparação do material é essencial para garantir resultados precisos. A superfície deve estar limpa e livre de sujeira, poeira ou óleo que possam interferir nas ondas ultrassônicas. O transdutor é então aplicado à superfície, geralmente com o uso de um gel ou líquido acoplante, que estabelece a conexão necessária entre o transdutor e o material.
5. Análise de Dados: Após a execução do teste, os dados obtidos são analisados por um técnico experiente. A interpretação dos resultados requer conhecimento técnico, uma vez que as reflexões das ondas podem indicar a presença de falhas ou indicar a espessura do material em pontos específicos.
6. Vantagens do Ultrassom: A inspeção por ultrassom possui várias vantagens, como a capacidade de fornecer informações em tempo real, ser aplicável a uma ampla gama de materiais e reduzir o tempo necessário para realizar inspeções detalhadas. Além disso, é um método sem riscos de contaminação, tornando-o ideal para ambientes industriais.
Em resumo, a inspeção por ultrassom é uma abordagem eficaz e confiável nos ensaios não destrutivos, garantindo a segurança e a qualidade em diversos setores, incluindo construção, petróleo e gás, e setores automotivos. Sua precisão e versatilidade fazem dela uma escolha preferencial para assegurar a integridade de materiais e estruturas.
Desafios e Limitações dos Ensaios Não Destrutivos
Embora os ensaios não destrutivos (END) ofereçam uma série de vantagens significativas, como a preservação do material e a detecção precoce de falhas, eles também enfrentam desafios e limitações que devem ser compreendidos para uma aplicação eficaz. Abaixo estão alguns dos principais desafios e limitações associados a esses métodos.
1. Treinamento e Qualificação: A interpretação dos resultados dos ensaios não destrutivos exige profissionais altamente qualificados. A falta de formação adequada pode levar a interpretações incorretas, resultando em falhas na identificação de problemas críticos.
2. Limitações de Materiais: Alguns métodos de END, como a radiografia e a inspeção por ultrassom, podem ter dificuldades com certos materiais ou geometrias complexas. Por exemplo, materiais muito finos ou altamente reflexivos podem afetar a clareza das imagens obtidas.
3. Custos e Equipamentos: Embora os END possam economizar dinheiro a longo prazo, os custos iniciais de equipamentos e treinamento podem ser altos. Além disso, a necessidade de manutenção e calibração frequentes dos equipamentos pode resultar em custos adicionais.
4. Tempos de Exame: A realização de ensaios não destrutivos pode ser demorada, especialmente para inspeções complexas ou em grandes estruturas. Isso pode levar a interrupções significativas nas operações, especialmente em setores onde o tempo de inatividade deve ser minimizado.
5. Dependência de Condições Ambientais: As condições ambientais, como temperatura, umidade e presença de contaminantes, podem afetar a eficácia de alguns métodos de END. Por exemplo, a presença de umidade pode interferir na precisão das medições ultrassônicas.
6. Limitações de Detecção: Nenhum método de END pode garantir a detecção de todas as falhas. Algumas descontinuidades podem passar despercebidas devido a ângulos de inspeção inadequados ou limitações técnicas do equipamento. Isso destaca a importância de uma combinação de métodos e uma estratégia de inspeção abrangente.
Apesar desses desafios, os ensaios não destrutivos continuam sendo uma ferramenta fundamental em diversas indústrias. Com a evolução contínua da tecnologia e o aumento na formação de profissionais, muitos desses desafios estão sendo abordados, melhorando a eficácia e a confiabilidade dos END.
Os ensaios não destrutivos (END) são fundamentais para a segurança e a eficiência nas operações industriais, proporcionando benefícios significativos, como a preservação de materiais e a detecção precoce de falhas.
Sua aplicação em setores como aeronáutica, construção e petroquímico demonstra sua relevância na manutenção da qualidade e integridade das estruturas.
Embora enfrentem desafios, como a necessidade de profissionais qualificados e limitações tecnológicas, os avanços na tecnologia e na formação têm contribuído para superá-los.
A escolha adequada do método de inspeção e a combinação de diferentes técnicas são essenciais para maximizar a eficácia dos ensaios não destrutivos.
Em resumo, a adoção de END não apenas garante a segurança e a funcionalidade de estruturas e componentes, mas também assegura conformidade com normas e regulamentos, promovendo a confiança entre consumidores e indústrias.
Assim, a continuidade dos investimentos e a pesquisa nesta área são vitais para o futuro da engenharia e da proteção industrial.