Teste de Solda Eletrodo Revestido: Como Realizar Corretamente
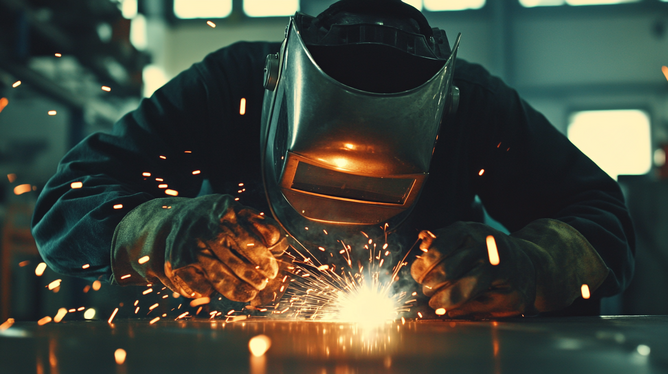
Por: João - 26 de Setembro de 2024
O teste de solda eletrodo revestido é uma etapa fundamental para garantir a qualidade e a durabilidade das juntas soldadas. Realizar o teste corretamente pode evitar problemas futuros e assegurar que as estruturas atendam aos padrões de segurança. Neste artigo, você aprenderá sobre a importância do teste, os passos para realizá-lo e como analisar os resultados, garantindo assim uma soldagem de alta qualidade. Continue lendo para se aprofundar nesse assunto essencial!
Importância do Teste de Solda Eletrodo Revestido
A soldagem é um processo crucial em diversas indústrias, e a solda eletrodo revestido é uma das técnicas mais utilizadas, especialmente em trabalhos de construção e manutenção de estruturas metálicas. Este método não apenas proporciona a união de diferentes partes metálicas, mas também exige precisão e cuidado para garantir a integridade da solda. O teste de solda eletrodo revestido torna-se, portanto, uma etapa indispensável. Neste texto, iremos explorar a importância desse teste, suas implicações e como ele pode afetar a qualidade do trabalho final.
Um dos principais motivos para realizar o teste de solda eletrodo revestido é garantir a qualidade da união soldada. Quando as peças metálicas são unidas, diferentes fatores podem influenciar a eficácia da solda, como a preparação das superfícies, a temperatura do material e a técnica utilizada pelo soldador. Por isso, o teste serve como um mecanismo de controle de qualidade que identifica falhas potenciais antes que se tornem problemas significativos.
Além da qualidade, a segurança é uma preocupação primordial na indústria. Estruturas mal soldadas podem levar a falhas catastróficas, colocando em risco não apenas a vida dos trabalhadores, mas também a integridade da obra. O teste de solda eletrodo revestido atua como uma salvaguarda, reduzindo o risco de falhas ao longo do tempo. Um resultado positivo no teste indica que a solda pode suportar as tensões e forças a que será submetida, conferindo maior segurança ao projeto.
A durabilidade das estruturas também é uma razão para a realização do teste de solda eletrodo revestido. Soldas mal feitas são suscetíveis à corrosão, fadiga e outras formas de degradação. Ao realizar os testes adequados, os profissionais podem não apenas confirmar a resistência imediata da soldagem, mas também prever a performance a longo prazo. A solda deve resistir ao estresse mecânico, variações de temperatura e elementos corrosivos do ambiente. Portanto, o teste é uma ferramenta vital para a previsão de durabilidade.
Outro aspecto importante é o gerenciamento de custos. Problemas com a soldagem podem levar a reparos dispendiosos e atrasos nas obras. Quando a qualidade da soldagem não é verificada, existe o risco de se ter que refazer o trabalho, o que não só eleva os custos mas também causa a perda de tempo e recursos. A realização de um teste de solda eletrodo revestido antes da finalização do projeto economiza dinheiro ao garantir que tudo esteja em conformidade desde o início.
O teste de solda eletrodo revestido também é essencial para assegurar a conformidade com normas e regulamentações. Muitas indústrias estão sujeitas a códigos específicos de segurança e qualidade, que exigem verificações de solda a fim de garantir a adesão a padrões estabelecidos. Realizar testes significa não apenas seguir as diretrizes, mas também assegurar a qualidade do produto final. Os resultados dos testes podem ser utilizados como documentação de conformidade e podem ser exigidos em auditorias ou avaliações de segurança.
Além disso, o teste oferece uma oportunidade para o aprimoramento profissional. Quando os soldadores podem ver os resultados de seu trabalho por meio de testes, eles podem identificar áreas para melhorar e se desenvolver como profissionais. O feedback dos testes de soldagem pode ser uma fonte de aprendizado, permitindo que eles se tornem mais habilidosos e confiantes em sua prática.
A variação nas condições de trabalho, como a umidade e a temperatura, também pode afetar a qualidade da solda realizada. Devido a essas variáveis, o teste de solda eletrodo revestido é uma maneira de verificar como diferentes condições impactam o resultado final. Esse feedback é valioso não apenas para o soldador, mas também para a gestão do projeto, pois indica a necessidade de ajustes ou reavaliações nas práticas de soldagem.
Os testes de solda podem ser realizados de várias maneiras, cada uma com suas peculiaridades. Entre os métodos comuns estão os testes não destrutivos, como a ultrassonografia, e testes destrutivos, que incluem a tração e a dobra. Esses métodos ajudam a assegurar que todos os aspectos da soldagem estejam de acordo com as exigências. Independentemente do método escolhido, o mais importante é que o teste seja realizado por profissionais qualificados, nos quais se pode confiar para interpretar os resultados adequadamente.
Por fim, é importante considerar que a realização do teste de solda eletrodo revestido não deve ser vista como uma tarefa opcional, mas como um componente essencial do processo de soldagem. A soldagem, quando realizada corretamente e testada, não apenas garante uma estrutura mais robusta, mas também contribui para a eficiência e a segurança da obra como um todo. Portanto, empresas e profissionais devem sempre priorizar esse tipo de teste como parte integrante de suas operações.
A importância do teste de solda eletrodo revestido se reflete na qualidade, segurança, durabilidade e custo total dos projetos realizados. Ao investir tempo e recursos para garantir que as soldas atendam aos padrões exigidos, as equipes podem proporcionar um valor duradouro e confiança em seu trabalho. Em um mundo onde a margem de erro é mínima e as exigências são máximas, não há dúvida de que o teste de solda deve ser uma prioridade.
Passo a Passo do Teste de Solda
Realizar o teste de solda eletrodo revestido é essencial para garantir a qualidade e a segurança das juntas soldadas. Abaixo está um guia detalhado que descreve o passo a passo para executar esse teste de forma eficaz. Cada fase é importante e deve ser seguida com rigor para assegurar que os resultados sejam confiáveis e que a solda atenda aos padrões de qualidade exigidos.
Passo 1: Preparação do Local de Trabalho
A preparação do local é o primeiro passo e deve ser realizada com cuidado. Um ambiente limpo e organizado é vital para evitar contaminações que possam comprometer a solda e os testes subsequentes.
- Escolha um local adequado: O espaço deve ser bem iluminado e arejado, longe de materiais inflamáveis.
- Limpeza da área: Remova qualquer sujeira, gordura ou resíduos da superfície onde a soldagem foi realizada.
- Verificação do equipamento: Certifique-se de que todos os instrumentos e ferramentas estão em condições adequadas de uso.
Passo 2: Seleção do Método de Teste
Existem diferentes métodos para testar soldas, e a escolha do método correto depende dos materiais envolvidos e dos requisitos específicos do projeto. Dentre os métodos mais comuns estão:
- Testes Destrutivos: Incluem tração, dobra e impacto, onde a solda é submetida a forças até falhar. Isso fornece dados sobre a resistência.
- Testes Não Destrutivos (NDT): Como a ultrassonografia e a radiografia, eles permitem avaliar a qualidade da solda sem comprometer sua integridade.
Passo 3: Execução do Teste Destrutivo
Se optar por um teste destrutivo, siga estas etapas:
- Corte a solda: Após a solda ter curado adequadamente, corte uma amostra representativa utilizando uma serra apropriada.
- Realize os testes: Dependendo do teste escolhido, use uma máquina de tração ou outro equipamento de teste especializado.
- Documentação: Anote todos os resultados, como a força máxima, o alongamento e qualquer falha observada.
Passo 4: Execução do Teste Não Destrutivo (NDT)
Para os testes não destrutivos, siga estas diretrizes:
- Ultrassonografia: Utilize um equipamento adequado para emitir ondas sonoras e capturar reflexões que indicam falhas internas.
- Radiografia: Posicione a fonte de radiação e o filme radiográfico corretamente para detectar imperfeições na solda.
- Outros métodos NDT: Métodos como correntes parasitas e teste de líquidos penetrantes também podem ser utilizados conforme a situação.
Passo 5: Análise dos Resultados
Após a realização dos testes, é hora de analisar os resultados. A interpretação correta desses dados é crucial para determinar a qualidade da solda.
- Documente os resultados: Registre os dados de forma sistemática e organizada para referência futura.
- Comparação com normas: Compare os resultados obtidos com os padrões estabelecidos pela norma técnica aplicável (ex: ABNT, AWS).
- Identificação de falhas: Caso existam falhas, classifique-as e determine as possíveis causas que levaram aos problemas.
Passo 6: Conclusão e Relatório Final
Após a análise, é importante seguir para a elaboração de um relatório final. Este documento deve incluir todos os aspectos do teste realizado.
- Sumário dos testes: Resuma todos os tipos de testes executados, incluindo as condições do teste e o método aplicado.
- Resultados detalhados: Inclua uma seção com resultados estatísticos e gráficos que evidenciem a performance das soldas.
- Recomendações: Conclua com recomendações caso os resultados não tenham sido satisfatórios, sugerindo nesse caso a necessidade de retrabalho ou revisão dos processos de soldagem.
Passo 7: Implementação de Melhorias
Com base nos resultados e nas recomendações do relatório, o próximo passo é implementar melhorias no processo de produção.
- Ajustes no treinamento: Ofereça treinamentos adicionais para os soldadores baseados nos dados coletados e nas falhas identificadas.
- Revisão de procedimentos: O procedimento de soldagem pode precisar de ajustes variados, conforme as falhas observadas durante os testes.
- Equipamentos: Se necessário, atualize o equipamento de soldagem ou de teste para tecnologias mais modernas e eficientes.
Passo 8: Monitoramento Contínuo
A implementação de um sistema de monitoramento contínuo após a realização dos testes é fundamental para garantir a qualidade da solda a longo prazo.
- Acompanhamento regular: Estabeleça um cronograma para a realização de testes periódicos, assegurando a manutenção da qualidade ao longo do tempo.
- Feedback contínuo: Crie uma cultura de feedback entre os soldadores e supervisores, incentivando melhorias e aprendizado mútuo.
- Atualizações sobre regulamentações: Mantenha-se informado sobre novas normas e práticas recomendadas para garantir a conformidade com os padrões da indústria.
Considerações Finais
Realizar o teste de solda eletrodo revestido seguindo esse passo a passo é uma maneira eficaz de assegurar a qualidade e a segurança das soldas executadas. Cada etapa é importante e contribui para um resultado final que atenda às expectativas e padrões exigidos. Ao investir tempo e recursos para realizar testes adequados, você protege seu projeto, assegurando que a solda não apenas atenda aos requisitos imediatos, mas também mantenha sua integridade ao longo dos anos. A prática de seguir essas diretrizes não só resulta em estruturas mais seguras e duráveis, mas também eleva o padrão de qualidade no setor de soldagem como um todo.
Equipamentos Necessários para Realizar o Teste
Ao realizar um teste de solda eletrodo revestido, a escolha dos equipamentos corretos é fundamental para garantir resultados precisos e confiáveis. Neste artigo, vamos explorar detalhadamente os diversos equipamentos necessários, suas funções e a importância de cada um deles no processo de teste. A utilização adequada dessas ferramentas contribui não apenas para a segurança do trabalho, mas também para a qualidade do resultado final.
Equipamentos básicos de soldagem
Antes de entrar nos equipamentos específicos para o teste, é essencial rever os equipamentos básicos de soldagem que influenciam diretamente a qualidade da união. Estes equipamentos incluem:
- Máquina de solda: Existem diferentes tipos de máquinas, como os inversores, transformadores e máquinas de solda MIG/MAG. Escolher a máquina adequada para o tipo de eletrodo e material a ser soldado é essencial para garantir uma boa penetração e a formação de uma solda de qualidade.
- Eletrodos revestidos: A escolha do tipo adequado de eletrodo tem um papel fundamental na qualidade da solda. Eletrodos de diferentes composições e espessuras podem impactar diretamente a resistência da solda.
- Máscara de solda: A proteção da visão é essencial. A máscara deve ser escolhida com base na sua capacidade de filtragem, protegendo o operador da radiação e do calor gerados durante a soldagem.
- Garra de aterramento: Esta peça é necessária para completar o circuito elétrico da máquina de solda, evitando choques e garantindo a segurança durante o trabalho.
- Cabos de soldagem: Utilizados para conectar a máquina ao eletrodo e à garra de aterramento. Devem ser compatíveis com a máquina e com a intensidade de corrente utilizada.
Equipamentos para Testes Destrutivos
Os testes destrutivos são aqueles que efetivamente afetam a integridade da solda. Aqui estão os principais equipamentos necessários para esses tipos de teste:
- Máquina de tração: Este equipamento é fundamental para testar a resistência da solda por meio de tensão. A amostra de solda é colocada na máquina e esticada até que ocorra a fratura. Analisar a força necessária para romper a solda fornece informações sobre sua resistência.
- Máquina de dobra: Utilizada para realizar o teste de dobra, que consiste em dobrar uma amostra soldada para avaliar a ductilidade e a flexibilidade da solda. A máquina deve ser calibrada, para que os resultados sejam precisos.
- Máquina de impacto: Este equipamento testa a resistência da solda sob um choque abrupto. A solda é submetida a uma força concentrada, e o resultado indica a resistência a condições extremas.
- Equipamentos de corte: Para os testes destrutivos, será necessário cortar amostras das soldas. Ferramentas como serra, serra fria ou plasma são essenciais para garantir cortes limpos sem causar danos adicionais à solda.
Equipamentos para Testes Não Destrutivos (NDT)
Os testes não destrutivos permitem avaliar a qualidade da solda sem comprometer sua integridade. Os principais equipamentos utilizados incluem:
- Máquina de ultrassom: Este equipamento emite ondas sonoras que percorrem a solda. Ao encontrar falhas internas, as ondas refletem de maneira diferente, revelando descontinuidades na solda. A ultrassonografia é extremamente eficaz para identificar falhas internas sem danificar a peça.
- Equipamento de radiografia: Utiliza radiação para criar imagens da solda em questão. A radiação penetra a peça soldada e o filme revela falhas internas. Este método é mais complexo e requer cuidado redobrado quanto à segurança e radiação.
- Equipamento para líquido penetrante: Este método utiliza líquidos que penetram em fissuras e descontinuidades. Após a aplicação, um revelador é adicionado, e as falhas se tornam visíveis. Esse método é eficaz para detectar falhas de superfície.
- Máquina de corrente parasita: Esse método consiste na geração de correntes elétricas que detectam descontinuidades nas soldas. Equipamentos que utilizam essa técnica são muito eficazes para identificar áreas com falhas em materiais ferrosos e não ferrosos.
Equipamentos de Medição e Avaliação
Além dos equipamentos de teste, existem vários instrumentos de medição que auxiliam na avaliação da solda:
- Calibrador de espessura: Fundamental para medir a espessura das passagens de solda e garantir que estejam dentro das tolerâncias especificadas no projeto.
- Paquímetro e micrômetro: Ferramentas utilizadas para medições precisas das dimensões da solda e das peças conectadas.
- Termômetro infravermelho: Utilizado para medir a temperatura da solda durante o processo de soldagem, garantindo que esteja dentro dos limites apropriados para a fusão do material.
- Máquina de ensaio de dureza: Utilizada para avaliar a dureza da solda e definir se ela atende aos requisitos de resistência pertinentes ao projeto.
Equipamentos de Segurança
A segurança é uma prioridade absoluta ao realizar testes de soldagem. Portanto, o uso de equipamentos de proteção individual (EPIs) é imprescindível para garantir a saúde e segurança dos operários:
- Óculos de proteção: Devem ser utilizados para proteger os olhos de faíscas, particulados e radiação UV durante os testes.
- Luvas de proteção: Utilizadas para proteger as mãos contra cortes e queimaduras durante o manuseio de peças metálicas e maquinários.
- Protetores auriculares: Podem ser necessários para proteger a audição em ambientes onde há níveis elevados de ruído devido às máquinas de teste.
- Uniforme apropriado: Roupa que não seja inflamável e que proteja contra calor e faíscas é essencial para a proteção do trabalhador.
Trilhas de Avaliação e Manutenção de Equipamentos
Os equipamentos utilizados nos testes de solda eletrodo revestido devem ser mantidos em boas condições para garantir resultados precisos. Aqui estão algumas práticas recomendadas:
- Calibração regular: Todos os equipamentos de teste devem ser calibrados periodicamente para garantir precisão nas medições. Isso deve ser feito conforme as orientações do fabricante ou normativas da indústria.
- Manutenção preventiva: Realizar manutenções preventivas nos equipamentos, verificando se há desgastes ou danos que possam prejudicar o desempenho. Isso inclui limpeza e substituição de peças gastas.
- Treinamento adequado do pessoal: Garantir que todos os operadores estejam familiarizados com os equipamentos e suas manutenções, recebendo treinamentos regulares que aumentem suas habilidades e conhecimentos.
Conclusão
Realizar o teste de solda eletrodo revestido exige uma série de equipamentos que vão desde as ferramentas básicas de soldagem até instrumentos de medição de alta precisão. A escolha e manutenção desses equipamentos são essenciais para garantir a qualidade da solda e a segurança do processo. Além disso, a utilização de equipamentos de proteção individual é fundamental para ressaltar a necessidade de um ambiente de trabalho seguro. Com as ferramentas corretas e boas práticas, é possível assegurar que as juntas soldadas atendam aos padrões de qualidade e segurança, resultando em projetos de alta confiabilidade.
Análise dos Resultados do Teste de Solda
A análise dos resultados do teste de solda eletrodo revestido é uma etapa crítica que determina a qualidade da soldagem e, consequentemente, a segurança e a durabilidade das estruturas construídas. Neste artigo, vamos abordar os principais aspectos que envolvem a interpretação dos resultados dos testes de solda, a importância de seguir parâmetros adequados e os métodos para garantir que essa análise seja realizada de forma eficaz.
1. Importância da Análise
A análise dos resultados dos testes de solda é essencial por várias razões:
- Garantia de qualidade: A análise permite verificar se a solda atende aos padrões de qualidade exigidos pelas normas técnicas e requisitos do projeto.
- Identificação de falhas: Testes eficazes permitem detectar falhas que poderiam comprometer a integridade estrutural, como fissuras, porosidade e falta de penetração.
- Segurança: A solda mal executada pode levar a falhas catastróficas. A análise garante que as estruturas sejam seguras para o uso, prevenindo acidentes.
- Feedback para melhoria: Os dados coletados e analisados podem oferecer informações valiosas para a fábrica e os soldadores, identificando áreas para melhorar a técnica e o procedimento de soldagem.
2. Métodos de Análise dos Resultados
As análises podem ser realizadas de diversas maneiras, dependendo do tipo de teste aplicado. Abaixo estão listedos alguns métodos comuns de análise de resultados:
2.1 Testes DestrutivosOs testes destrutivos, apesar de comprometerem a integridade do material, fornecem dados diretos sobre a performance da solda. Alguns métodos de análise são:
- Teste de Tração: Os resultados devem ser comparados com os valores de especificação de resistência do material. A análise envolve avaliar a carga máxima suportada antes da fratura e o alongamento da amostra. Além disso, a fratura deve ser examinada, verificando sua natureza e se houve falhas.
- Teste de Dobra: A amostra é submetida a diferentes ângulos de dobra e a análise se concentra em detectar quaisquer trincas ou falhas visíveis na superfície do material. A análise também deve levar em consideração a resistência à dobra, em conformidade com as normas aplicáveis.
- Teste de Impacto: Avalia a energia absorvida pela solda durante a ruptura sob carga de impacto. Os resultados precisam ser comparados com especificações e normas para assumir que a solda está adequada para suportar impactos relevantes.
Os métodos não destrutivos são essenciais para a avaliação da solda sem danificá-la. Entre os métodos estão:
- Ultrassonografia: Os resultados são analisados identificando reflexões das ondas sonoras no interior do material. A presença de descontinuidades pode ser quantificada e a profundidade das falhas detectadas é também crucial para a análise.
- Radiografia: As imagens obtidas devem ser avaliadas em busca de defeitos internos como porosidade, inclusões e falhas de fusão. É fundamental que sejam observadas as densidades radiográficas para a identificação de falhas com precisão.
- Liquido Penetrante: Após a aplicação do penetrante e do revelador, a análise deve focar em identificar descontinuidades na superfície, que se tornam visíveis pela mudança de cor no material. A qualidade do acabamento da superfície e a definição das falhas são aspectos importantes a considerar.
- Correntes Parasitas: O método requer a análise da corrente gerada na peça e a avaliação da variação resultante. As leituras indicando descontinuidades devem ser documentadas e comparadas com os padrões estabelecidos.
3. Interpretação dos Resultados
A interpretação dos resultados de testes de solda deve ser baseada em critérios técnicos e normativos. Aqui estão algumas diretrizes essenciais:
- Referência a Normas: Sempre compare os resultados com as normas aplicáveis e as especificações do projeto. Normas como a AWS (American Welding Society) ou as da ABNT (Associação Brasileira de Normas Técnicas) oferecem critérios claros que devem ser seguidos.
- Classificação de Defeitos: As falhas detectadas devem ser classificadas. Defeitos menores podem não necessariamente comprometer a solda, enquanto falhas significativas podem exigir refação.
- Natureza das Falhas: A análise deve investigar a causa das falhas (ex: falta de penetração, porosidade, trincas) para que medidas corretivas possam ser aplicadas.
- Análise Estatística: Se indicadores de falhas recorrentes forem encontrados, pode ser útil realizar uma análise estatística dos dados para entender padrões que possam resultar em problemas constantes.
4. Documentação dos Resultados
Registrar os resultados de maneira organizada é crucial. Uma boa documentação deve incluir:
- Resultados Numéricos: Todos dados coletados devem ser registrados com precisão, incluindo valores de resistência, ângulos de dobra e detecções de falhas.
- Imagens e Gráficos: Sempre que possível, utilize imagens e gráficos para ilustrar os dados dos testes. Isso facilita a compreensão e análise dos resultados.
- Relatórios de Análise: Após completar a análise, prepare um relatório que sintetize os resultados, as interpretações e as recomendações para futuras soldagens.
- Histórico de Testes: Manter um registro histórico dos testes realizados e seus resultados pode ser valioso para comparação em testes futuros e avaliação do desempenho ao longo do tempo.
5. Recomendações Pós-Análise
Com base nos resultados obtidos e na análise realizada, recomendações devem ser criadas para as próximas etapas. Isso pode incluir:
- Treinamento de Pessoal: Se foram encontradas falhas relacionadas a técnicas de soldagem, pode ser necessário realizar treinamentos adicionais para os soldadores.
- Ajustes nos Processos: Reavaliação dos procedimentos de soldagem pode ser necessária. Ajustar a técnica, a temperatura ou a escolha de materiais pode resultar em soldas de melhor qualidade.
- Análises Periódicas: Realizar testes de solda regularmente pode ajudar a manter os padrões de qualidade, permitindo identificar e corrigir problemas antes que eles se tornem críticos.
- Atualizações Tecnológicas: Avaliar novas tecnologias e equipamentos que possam melhorar o processo de soldagem e os testes realizados.
6. Conclusão
A análise dos resultados dos testes de solda eletrodo revestido é uma etapa vital que assegura não apenas a qualidade da solda, mas também a segurança das estruturas em que elas são aplicadas. Com o uso de métodos adequados e uma interpretação criteriosa, é possível obter dados que oferecem feedback valioso para o processo de soldagem, guiando melhorias e evitando falhas futuras. A atenção aos detalhes, a documentação cuidadosa e a busca contínua por aprimoramento são essenciais para garantir a excelência na soldagem e a confiança nas obras realizadas.
Em conclusão, o teste de solda eletrodo revestido desempenha um papel indispensável na garantia da integridade e segurança das juntas soldadas. Compreender e dominar as etapas de realização e análise dos testes não apenas previne problemas futuros, mas também assegura que as estruturas construídas sejam de alta qualidade e duráveis. Ao seguir os procedimentos adequados e utilizar os equipamentos corretos, é possível manter padrões elevados e responder às exigências das normas técnicas. À medida em que você aplica as práticas discutidas neste artigo, ficará mais capacitado para enfrentar os desafios da soldagem e contribuir para a construção de obras seguras e confiáveis. Não subestime a importância dessa etapa; um teste eficaz é o primeiro passo para um trabalho de excelência.